The Science That’s Disrupting Construction Progress Tracking in 2025
Despite all the advances in project management software, construction consultants and contractors still face the same issues: Traditional tools like MS Project or Primavera only track start/finish dates and percent complete. But real project risk happens between those milestones, in the daily site activities, delays, rework, and sudden changes. The Breakthrough Consultants & Contractors Can’t Afford to Miss Professor Tarek Hegazy, one of North America’s most cited civil engineers, has led groundbreaking work in automated progress tracking. Two of his research papers introduced automated progress tracking and the Critical Path Segments (CPS) method to capture real-time site activity and mid-activity delays. What’s inside: Read the Full Review A must-read for contractors, consultants, and PMOs aiming to modernize their approach to progress tracking. This is not just theory. It’s the foundation for real-world solution, now powering the most forward-thinking consultant and contractor teams in the industry including Dar Al Handasah & Verve Projects.
Progress Tracking Maturity Checklist
Tick the boxes below and find out how mature your progress tracking system really is. 1. Planning Accuracy Baseline schedules are updated and actively used Lookahead plans are integrated into the master schedule Critical path is clearly defined and reviewed regularly 2. Data Collection Progress is captured daily or weekly with evidence Updates follow a standardized format Site staff are trained in data collection tools 3. Real-Time Visibility I can access live data without calling the site I can see progress % at multiple levels I receive daily/weekly dashboards automatically 4. Delay Detection Slippage is detected before it hits critical path I have early warning signals (e.g., S-curves) Recovery plans are created and monitored 5. Reporting Reports are auto-generated (not in Excel) Stakeholders have tailored report views Reports are visual and explain delays with clarity 6. Accountability Every task has a responsible party & deadline I can track who delayed what Delays are escalated and followed up automatically 7. Forecasting I can forecast completion dates accurately Forecasts are based on actual site data Forecasts consider productivity trends 8. Resource Management I know daily labor and equipment availability Resource allocation is linked to progress tracking 9. Subcontractor Tracking I can track subcontractor-specific progress Subcontractors are accountable to dates and milestones 10. Earned Value Analysis I track planned vs actual progress vs cost I use CPI and SPI to guide decisions 11. Automation & Integration My tracking system integrates with scheduling & cost tools Calculate Score
Performance Certificate in Construction: A Passport to Safe Harbor
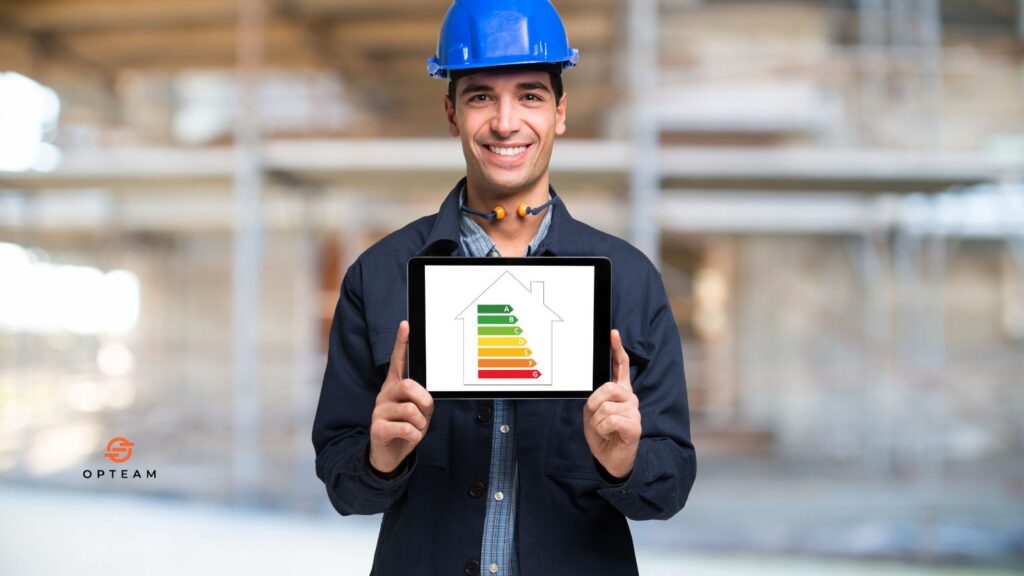
In the world of construction, where deadlines, budgets, and safety all collide, one document can mean the difference between smooth project closure and serious legal risk: the Performance Certificate. Nicknamed by many as the “passport to safe harbor”, this certificate plays a pivotal role in contract completion, payment release, and project accountability. Yet, it’s one of the most misunderstood—and often delayed—documents in the entire project lifecycle. This article breaks it all down in simple terms. Whether you’re a contractor, consultant, developer, or project manager, you’ll leave with a clear understanding of: Let’s get started. What Is a Performance Certificate? A Performance Certificate is a formal document issued by the contract administrator (often the consultant, engineer, or architect) that confirms the contractor has met the contractual requirements for practical completion. Think of it as the official acknowledgment that the contractor has done their job—at least to the extent that the project can now be handed over to the client and occupied or used as intended. It typically includes: Why It’s Called “A Passport to Safe Harbor” In maritime terms, a safe harbor is a secure place for a vessel to dock during stormy conditions. In construction, the Performance Certificate is that harbor—for both the contractor and client. Here’s why: No wonder it’s often called the most important piece of paper at the end of a project. The Performance Certificate vs. Other Certificates It’s easy to confuse the Performance Certificate with other common certificates. Here’s how it stacks up: Certificate Purpose Issued By When Completion Certificate Confirms entire project is complete, including final handover Consultant or Engineer End of contract Practical Completion Certificate Confirms project is ready for use with minor defects Consultant or Engineer Before final completion Performance Certificate Confirms contractor fulfilled performance obligations during the defects liability period Consultant or Engineer After defects liability period ends Maintenance Certificate Confirms rectification of all defects during DLP Sometimes used instead of Performance Certificate End of DLP Note: In some jurisdictions (e.g., UAE, UK, Singapore), the terms can overlap or vary depending on the standard form of contract (FIDIC, JCT, NEC, etc.). When Is the Performance Certificate Issued? The Performance Certificate is not issued at handover. It typically comes: What Happens After It’s Issued? Why the Performance Certificate Matters So Much Let’s break it down by stakeholder: For Contractors: Without it, you’re still technically on the hook for the building. For Clients: No certificate? Then any future dispute can become a costly legal battle. For Project Managers and Consultants: Risks of Delaying the Performance Certificate Many construction firms take the Performance Certificate for granted—and it costs them. Here’s what can go wrong: What Can Delay a Performance Certificate? Several things can hold it up: Reason Description Unresolved Defects If snag items are pending or not fully rectified Missing Documentation As-built drawings, O&M manuals, warranties Client Non-Cooperation Delayed inspection requests or sign-off Administrative Oversights The supervising consultant simply forgot Unclear Procedures Different interpretations of contract closeout terms Pro Tip: Keep a close-out checklist from day one. Don’t wait for the DLP to end. How to Secure Your Performance Certificate Faster Here’s how to avoid the waiting game: 1. Maintain a Defects Log Throughout DLP Don’t wait until the end of the DLP to fix defects. Track them live, respond promptly, and update status weekly. 2. Schedule Mid-DLP Reviews Treat it like a mini-inspection midway through the DLP. This shows commitment and uncovers issues early. 3. Submit Final Documentation in Advance Prepare O&M manuals, warranties, and certifications before the DLP ends. Get client and consultant feedback early. 4. Use a Certificate Tracker Use project management software (like Opteam) that tracks all certification stages and flags bottlenecks. 5. Keep the Consultant Engaged Invite the consultant to monthly status updates, even after handover. Keep them close—because they issue the certificate. Real-World Example: Dubai Marina Tower Case Let’s take a look at a real example. In a real case before the Abu Dhabi Court of Cassation, a subcontractor completed their contractual works but was denied the final retention payment of AED 693,384.29, as the final handover certificate had not been issued. What Happened: The Court’s Reasoning: Why It Matters: This case clearly shows how delays in issuing the performance or final handover certificate can have serious financial consequences — even if the contractor believes the job is done. It also reinforces that: Performance Certificate in FIDIC Contracts In FIDIC Red Book and Yellow Book contracts, the Performance Certificate is issued at the end of the Defects Notification Period (DNP)—equivalent to DLP. Here’s how FIDIC defines it: “The Engineer shall issue the Performance Certificate within 28 days after the latest of the expiry dates of the Defects Notification Periods…” This clause puts the burden on the Engineer, but in practice, the contractor must: You can’t sit and wait for the clock to run out. Key Takeaways If you’re skimming, here’s what matters most: Your Passport to Safe Harbor—Literally Construction is filled with risk. From budget overruns to unexpected delays, there’s always something that can go wrong. But the Performance Certificate is your shield at the end of the road. Get it. File it. Celebrate it. Because when it’s in your hands, it means: ✅ You’ve delivered✅ You’re paid✅ You’re off the hook✅ And your reputation remains intact Bonus Resource: Closeout Checklist Template To make your life easier, here’s a simple checklist to track progress toward earning your Performance Certificate: Performance Certificate Closeout Checklist Final Words Construction is a tough business. But you don’t have to leave money—or reputation—on the table just because of one missing document. Treat the Performance Certificate like your project passport. Get it stamped. And sail into safe harbor.
Performance Bond in Construction: The “Construction Bodyguard”
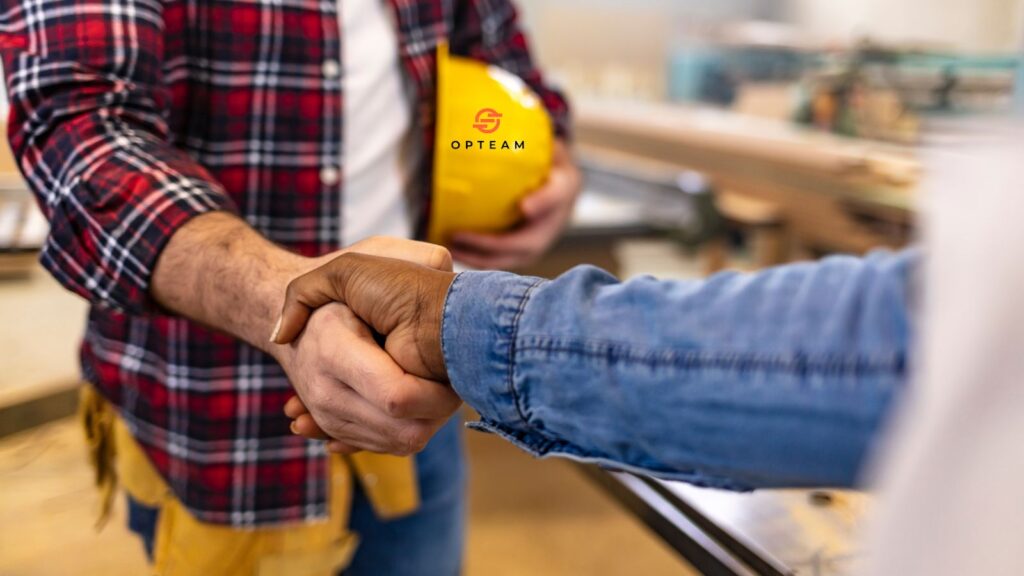
In construction, things don’t always go as planned. A contractor might delay the work, do a poor job, or even walk away before finishing. That’s where a performance bond comes in. Think of it like a bodyguard for the project. It doesn’t stop problems from happening, but it steps in when they do. If the contractor fails to deliver, the bond makes sure the work gets done—either by paying for the damages or bringing in someone else to finish the job. It’s a simple way to protect the owner’s money, time, and peace of mind. No big risks, no blind trust—just a safety net built into the contract. What is a Performance Bond in Construction? A performance bond is a written guarantee—usually from a bank or insurance company—that promises the contractor will complete the project according to the contract. If the contractor fails to deliver (for example, they go bankrupt or walk off the job), the performance bond steps in. It protects the project owner by either: 🔒 In Simple Terms: A performance bond is like a backup plan that says: “If the contractor messes up, we’ve got your back.” Why Are Performance Bonds Important? Construction projects involve high stakes: large budgets, strict deadlines, and complicated scopes of work. Any delay or failure can cause major financial loss. Key Reasons for Using Performance Bonds: How Does a Performance Bond Work? Step-by-Step Overview: Types of Construction Bonds (and How They Relate) Performance bonds are often part of a broader bond package. Here are the main types: 1. Bid Bond 2. Performance Bond 3. Payment Bond 4. Maintenance Bond (sometimes called a warranty bond) When Are Performance Bonds Required? Performance bonds are often required in the following situations: Performance Bonds in the GCC Construction Market In the GCC region (UAE, Saudi Arabia, Qatar, etc.), performance bonds are widely used and often required by law or regulation. Common Practices in GCC: Legal Basis: In many GCC countries, performance bonds are referenced in standard forms of contract like: What Does a Real Performance Bond Document Look Like? A performance bond is a formal legal document. It typically includes: Costs of Performance Bonds Performance bonds are not free. The cost is typically paid by the contractor and depends on several factors. Factors That Influence Cost: Typical Cost Range: What Happens If the Contractor Defaults? When a contractor defaults: This process can take weeks or months, depending on the complexity of the claim. Pros and Cons of Performance Bonds Pros for Project Owners: Cons for Project Owners: Pros for Contractors: Cons for Contractors: Common Misunderstandings 1. It’s Not Insurance A performance bond protects the project owner, but the surety can go after the contractor for repayment if a claim is paid. 2. It Doesn’t Cover Everything The bond only covers what’s in the contract. It won’t help if the owner changes the scope without proper documentation. 3. It Doesn’t Replace Project Management Having a bond doesn’t mean you can ignore site issues. Regular monitoring is still essential. Final Thoughts A performance bond in construction is one of the most important tools for managing risk. It acts like a “construction bodyguard,” protecting owners from financial loss when things go wrong, while also keeping contractors accountable. Whether you’re a project owner in Riyadh, a developer in Dubai, or a contractor taking on a large job in Doha, understanding performance bonds is key to building with confidence.
Milestone Billing vs Progress Billing in Construction
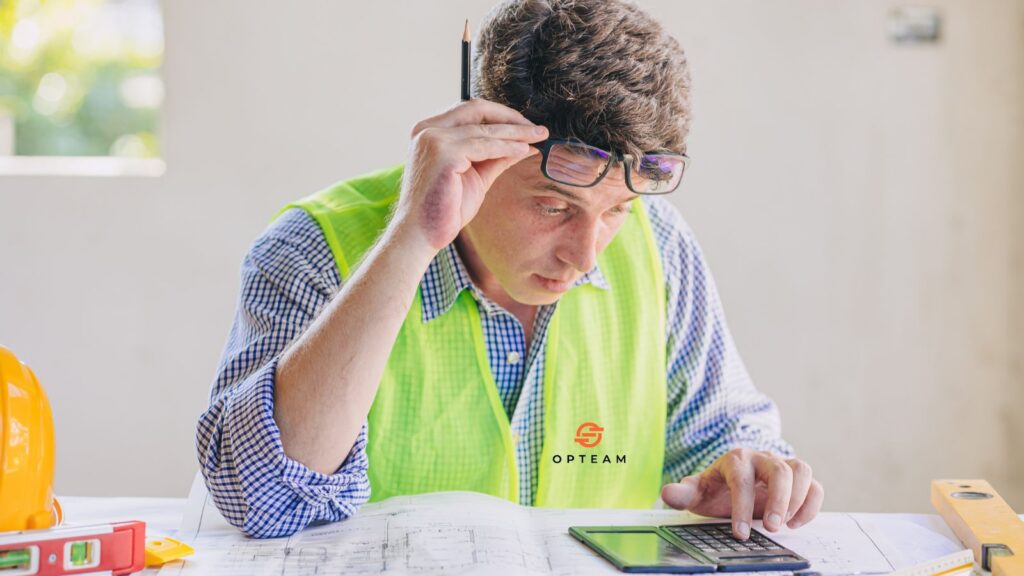
In construction, both milestone billing and progress billing are common methods used to invoice clients throughout a project—but they differ in how and when payments are triggered. Milestone billing ties payments to specific project achievements (like completing the foundation or reaching handover), while progress billing is based on the percentage of work completed over time. Each method offers distinct advantages depending on the project scope, risk tolerance, and cash flow needs. Milestone Billing vs Progress Billing in Construction: Deep Dive Aspect Milestone Billing Progress Billing Definition Invoices are issued when predefined project milestones are achieved. Invoices are issued based on the percentage of work completed. Trigger for Payment Completion of specific deliverables or stages (e.g. foundation done). Ongoing work measured regularly (e.g. weekly or monthly updates). Billing Frequency Less frequent, tied to major milestones. More frequent, usually monthly or bi-weekly. Measurement Basis Objective, milestone-based (e.g. “Phase 1 complete”). Subjective, based on % of work done or earned value reports. Cash Flow Impact Cash flow can be lumpy, with large payments after each milestone. Smoother, more predictable cash flow over time. Risk Allocation Shifts more risk to the contractor (delays = delayed payments). Spreads risk over time, aligns payments with actual work progress. Best For Projects with clear phases or long gaps between deliverables. Projects with continuous work and steady progress. Examples High-rise building: payment after excavation, structure, MEP, etc. Road construction: billed monthly based on linear meters completed. Owner Visibility Less frequent updates; focuses on major outcomes. More detailed, ongoing visibility into project status. Administrative Burden Lower, fewer invoices to manage. Higher, requires regular documentation and approvals. Why Billing Methods Matters in Construction Choosing between milestone billing and progress billing isn’t just about how you get paid—it directly impacts how you track progress on site. With milestone billing, your project needs clear checkpoints and robust documentation to prove when each phase is complete. On the other hand, progress billing demands continuous tracking of work performed, quantities completed, and real-time reporting to justify invoices. In both cases, accurate and transparent progress tracking is the backbone of timely payments, stronger cash flow, and better trust with clients. Without it, billing becomes guesswork—and guesswork leads to disputes, delays, or rejected invoices. That’s why modern construction teams are investing in digital tools that automate progress tracking and tie it directly to their billing workflows. Financial Impact of Poor Progress Tracking on Construction Billing In construction, billing isn’t just about sending invoices—it’s about proving work was done. When progress tracking is weak, everything else unravels: cash flow stalls, payments get delayed or rejected, and trust with the client erodes. Poor tracking often means relying on outdated spreadsheets, vague site reports, or estimations that don’t reflect reality. This disconnect between what’s been done on-site and what’s being billed leads to: Ultimately, poor progress tracking turns billing into a gamble instead of a process. The solution? Implementing real-time, accurate tracking systems that connect field updates directly to invoicing. When you can back every invoice with clear, time-stamped progress data, payments flow faster—and so does project momentum. Tools and Tech That Simplify Progress Tracking for Billing Teams Gone are the days of chasing WhatsApp photos, Excel sheets, and handwritten notes to justify a construction invoice. Today, the smartest teams are leaning on construction tech platforms that automate progress tracking and tie it directly to billing workflows—saving time, reducing disputes, and improving cash flow. Here are some of the top tools making that possible: Opteam (Built for GCC Contractors) Opteam offers real-time, visual progress tracking tailored specifically for construction projects in the region. Site teams can log daily progress using photos, checklists, and actual quantities—all from their phones. What sets Opteam apart is its automated linkage between progress and billing, allowing project managers to generate accurate billing reports without manual calculations. No more guessing or back-and-forth with finance. Procore A global construction management platform that includes progress tracking modules. While more comprehensive, it can be heavy for small to mid-sized projects. Great for firms needing integration across all project workflows, from RFIs to invoicing. LetsBuild Focused on site execution and coordination, LetsBuild allows teams to record task progress and tie it to project timelines. Its structured reporting is useful for progress claims but may need customization for complex billing setups. Autodesk Build (formerly BIM 360) Offers advanced progress tracking features, especially when paired with 3D models. Best suited for projects that use BIM and require granular control and documentation. Planyard A budgeting and cost control tool with integrated progress tracking and invoice verification. It’s particularly useful for finance teams looking to cross-check subcontractor billing with actual site progress. Why This Matters When progress tracking is automated and directly tied to billing: If your billing team is still chasing updates manually, it’s not just inefficient—it’s expensive. The right tool can turn daily site activity into billable, verifiable progress without the headache.
TOC Meaning in Construction
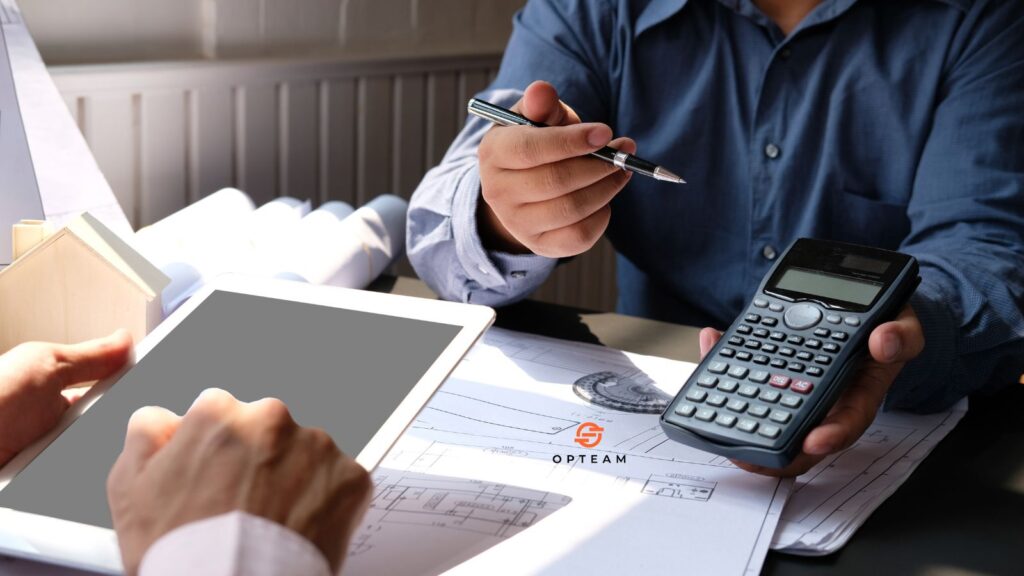
TOC in construction stands for Total Outturn Cost. It refers to the final and complete cost of a construction project, including not just the initial construction expenses, but also all the additional costs that come up along the way—like design changes, site issues, delays, permits, and even post-completion adjustments. In simple terms, TOC is the true cost of delivering a project, from start to finish. It’s what the project ends up costing in reality—not just what’s written in the original budget. Importance of TOC in Construction Understanding the Total Outturn Cost (TOC) is essential for successful project delivery in construction. It gives stakeholders a complete picture of how much a project truly costs—beyond the initial contract value. This includes variations, unforeseen expenses, and operational considerations that often arise during execution. Without a clear view of TOC, project managers risk underestimating the financial scope, which can lead to budget overruns, disputes, and compromised project outcomes. Moreover, TOC plays a crucial role in benchmarking and future project planning. When organizations accurately track and analyze TOC across multiple projects, they build a data-driven foundation for improving cost estimates and reducing financial risks in future developments. According to the UK Government Infrastructure and Projects Authority, embedding TOC thinking early in the project lifecycle helps align commercial strategies with realistic financial expectations, leading to better value for money and improved long-term asset performance. How to Accurately Estimate TOC in Construction Projects Let’s be real—estimating the Total Outturn Cost (TOC) of a construction project isn’t just about adding up materials and labor. It’s about predicting the real, final price tag of the whole thing, including all the unexpected twists and turns that always seem to pop up. Think design changes, delays, site surprises, regulation updates—yeah, all of that. So how do you get closer to the actual number without pulling your hair out? Start early and be brutally honest with your assumptions. Base estimates on real, historical data—not wishful thinking. The more similar projects you can reference, the better. Involve your whole team too: planners, engineers, quantity surveyors—they all see different parts of the cost picture. And don’t forget risk allowances. That’s where many TOC estimates fall short. Use tools that let you track budget shifts in real time so you’re not blindsided later. Whether it’s spreadsheets or project controls platforms like Opteam, the goal is the same: visibility. The more you see, the better you can plan. Common Factors That Inflate TOC in Construction Factor Why It Inflates TOC Scope Changes Mid-project design tweaks or added features mean more materials, time, and labor. Project Delays Every extra day costs money—equipment rental, labor, and sometimes penalties. Poor Risk Planning Unexpected site issues, weather, or regulatory hurdles can lead to unplanned expenses. Inefficient Resource Use Overstaffing, underutilized equipment, or bad scheduling eats into the budget. Material Price Fluctuations Global markets shift fast—what cost $100/unit today might be $140 next month. Contractor Claims & Disputes Legal or payment issues can stall progress and add admin/legal costs. Low-Quality Work Rework or defects discovered later = double spending to fix what should’ve been right. Inaccurate Initial Estimates Starting with an unrealistic baseline sets the whole budget off track. TOC vs Contract Value: Why the Difference Matters When managing construction projects, it’s important to understand the difference between the Total Outturn Cost (TOC) and the Contract Value—because they’re rarely the same. The contract value is the price agreed upon at the start of the project. It typically covers the defined scope of work and is often used as a benchmark for project delivery. On the other hand, TOC represents the actual final cost of the project, including everything from design changes and delays to inflation, claims, and rework. While the contract value sets expectations, TOC tells the full financial story. This gap between the two numbers can have serious implications. If the TOC significantly exceeds the contract value, it often points to cost overruns, scope creep, or poor risk management. That’s why tracking TOC in real time is becoming a growing priority for owners and project managers alike. Relying solely on the contract value can give a false sense of control, while TOC highlights the true financial exposure. Understanding and managing the difference between TOC and contract value isn’t just about controlling costs—it’s about protecting profit margins and improving forecasting for future projects. For example, this guide from Pinsent Masons explains how TOC can be used to resolve disputes and inform better decision-making. By making TOC a core part of your project controls strategy, you gain visibility into how well the project is really performing, which is crucial for both commercial success and long-term planning. Using Technology to Monitor and Control TOC in Real Time Let’s face it—managing construction costs manually is like trying to drive with your eyes half closed. You might stay on the road for a while, but it’s risky and things can go wrong fast. That’s where tech steps in. With the right tools, you can monitor and control your Total Outturn Cost (TOC) in real time, not weeks later when it’s too late to fix anything. Modern construction software lets you track budgets, cost forecasts, changes, and actual spending all in one place. Platforms like Opteam give you a live view of where your project financially stands—what’s been spent, what’s coming, and what’s creeping out of control. Real-time cost dashboards, automated progress tracking, and smart alerts mean you can respond faster to issues and avoid surprises. It’s not just about saving money—it’s about making smarter decisions as the project evolves. In a world where one delay or design tweak can cost thousands, that kind of visibility is a game changer.
How Much Does Construction Management Software Cost?
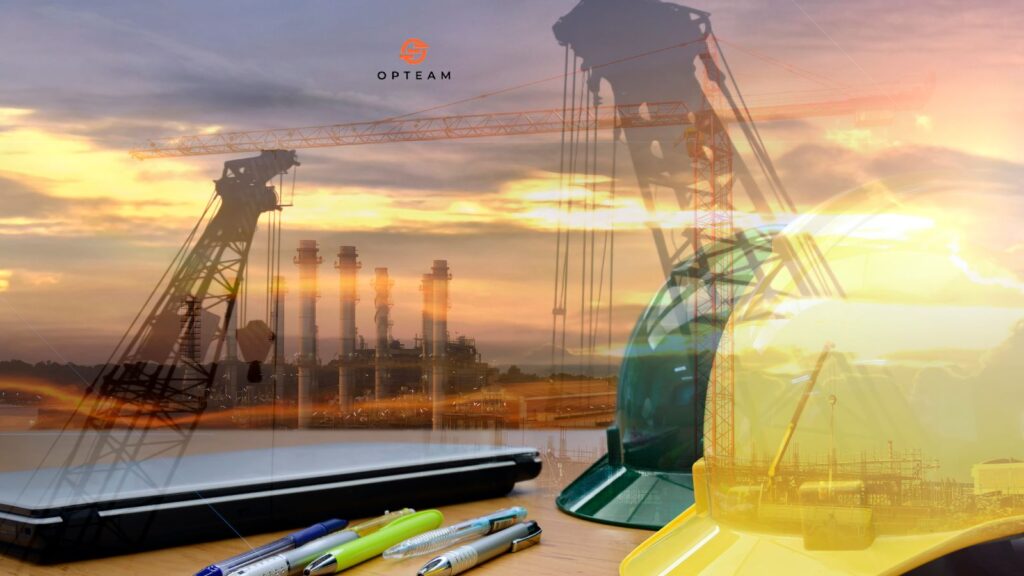
If you’re considering investing in construction management software, the first question you’re probably asking is: “How much is this going to cost us?” Straight answer? At Opteam, we offer two simple pricing models based on how your team runs projects: But cost isn’t just a number — it’s about value, usability, and fit for your workflow. Let’s break down what you’re really paying for — and what you should expect in return. 🔍 What Are You Actually Paying For? Most construction software charges for things you may or may not use. We don’t. With Opteam, you’re paying for one thing:Clarity. In your costs. In your progress. In your margins. Our pricing reflects the features that directly impact project profitability: In short: You’re not paying for dashboards — you’re paying to know if you’re making money. 🧑🔧 Option 1: $200/User/Month – Built for Nimble Teams This is perfect for: What you get: 👉 Example: A team of 5 would pay $1,000/month, no hidden fees. 🏗️ Option 2: Custom Per Project Pricing – Built for Volume If you’re managing multiple large-scale jobs at once, per-project pricing gives you predictable spend at scale. This is ideal for: Why it’s custom: 📞 Book a demo to get a custom quote in 30 minutes or less. 🆚 What About Cheaper Software? Sure — you can find cheaper tools. Some start at $50–100/month. But here’s the honest truth:Most of them give you features without outcomes. Fancy Gantt charts. Click-heavy workflows. Endless data entry. Field teams won’t use them. And leadership won’t trust them. Opteam is different: 💡 What’s the ROI of Using Opteam? Let’s say you prevent just one $10K overrun per project thanks to better tracking and forecasting. That’s 50x ROI for a small team using Opteam.And that’s not an exaggeration — we’ve seen teams hit that in their first month. 🏁 Bottom Line If you’re shopping for construction management software, here’s the simple breakdown: Plan Best For Cost Setup Time Notes Per User Small to mid-sized teams $200/user/month Under 24 hrs Unlimited projects Per Project Larger or scaling teams Custom quote Varies Tailored to job count & needs Ready to See the Numbers for Your Team? 📞 Book a demo — we’ll show you exactly what Opteam would cost, and exactly how much it could save you. Or, if you’re ready to roll:💳 Start with per-user pricing now and create your free account → Click here
Fastest Growing Construction Scheduling Analytics Software in the Industry
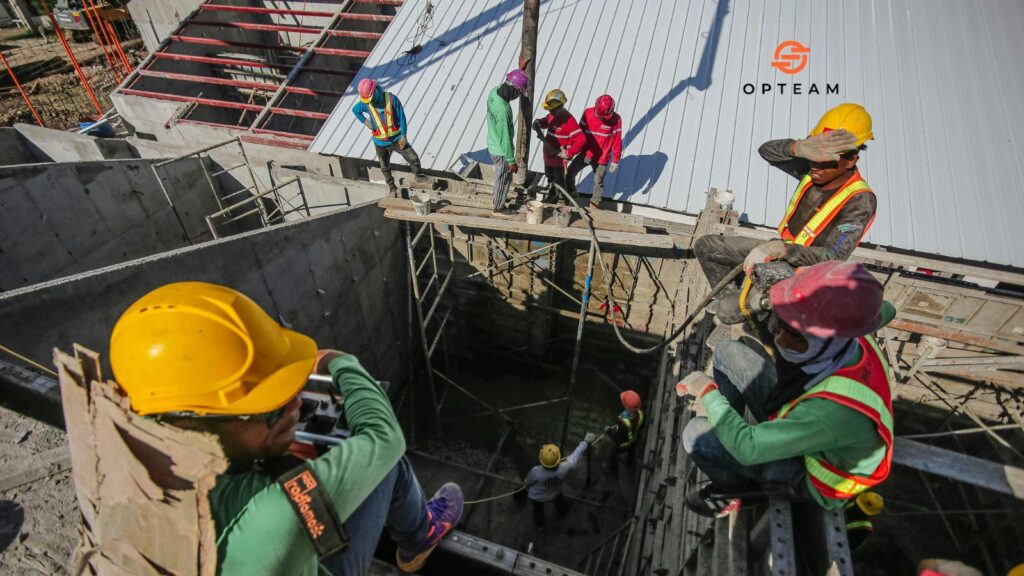
In construction, timelines are tight, budgets are tighter, and project complexity is at an all-time high. Among the chaos of change orders, material delays, subcontractor coordination, and cost overruns—one thing becomes crystal clear: spreadsheets and static Gantt charts aren’t enough anymore. Enter construction scheduling analytics software—a game-changer for contractors, planners, and project managers who want to stay ahead of the curve, not scramble to catch up. If you’re still using Primavera P6 or Excel to track your schedules, you’re not alone—but you’re also not optimized. ✅ Want to see how Opteam helps construction teams automate scheduling analytics and stay ahead of delays? Try it free for 14 days What Is Construction Scheduling Analytics Software? Construction scheduling analytics software is a category of digital tools that allow construction professionals to not only plan and track schedules—but analyze them. That means real-time insights into schedule performance, forecasting delays before they happen, identifying critical bottlenecks, and comparing planned vs. actual progress using smart, visual dashboards. In short: It’s the difference between “tracking a schedule” and “controlling your project’s future.” Key Features You Should Expect: Why Traditional Tools Fall Short Primavera P6 and Excel were great—20 years ago. But today’s projects demand a level of visibility, automation, and speed those tools can’t keep up with. Let’s break down what’s missing: Feature Primavera / Excel Construction Scheduling Analytics Software Real-time schedule updates ❌ Manual ✅ Automated Delay risk forecasting ❌ None ✅ Predictive Collaboration with site teams ❌ Disconnected ✅ Integrated Visual dashboards ❌ Static ✅ Interactive Time-saving automation ❌ Zero ✅ Built-in If your project schedule is only as accurate as your last update—you’re flying blind. 🔍 Stop relying on static files and guesswork. Get instant project visibility with Opteam The ROI of Smarter Scheduling Think analytics is just a “nice-to-have”? Let’s talk numbers. McKinsey reports that large construction projects typically take 20% longer to finish than scheduled and are up to 80% over budget. Most of these issues stem from poor planning and lack of real-time visibility. By using construction scheduling analytics software, companies have reported: When every day on site costs money, better scheduling = bigger profits. Use Case: How Opteam Helps Real Projects Stay on Track Let’s say you’re managing a high-rise residential tower with 18 months to deliver. Midway through the project, material delivery delays push back your slab casting schedule. Normally, this would trigger a chain reaction—subsequent trades like MEP and finishing crews fall behind, and the project starts bleeding days and money. With Opteam’s construction scheduling analytics software, you: That’s not managing chaos. That’s leading with confidence. 📊 Want to simulate delay impact with one click? Sign up for Opteam now How Opteam Stands Out Not all scheduling analytics tools are created equal. Here’s what makes Opteam the preferred choice for modern construction teams: 1. Instant Primavera & Excel Integration Upload your XER files or Excel schedules and get instant dashboards. No need to rebuild schedules from scratch. 2. Critical Path Segments™ (CPS) Methodology Opteam introduces a new, smarter way to monitor progress by segmenting your critical path and automatically showing where you’re falling behind. 3. Visual Delay Alerts See exactly which activities are slipping and how they affect the overall timeline. 4. Daily Reporting from Site to Schedule Integrate field updates with planning data. No more chasing WhatsApp updates from the site. 5. Works for Teams of Any Size Whether you’re a local contractor or managing a mega project, Opteam scales with you. ⚡ Ready to replace delay chaos with clarity? Start your free trial Who Needs Construction Scheduling Analytics Software? This isn’t just a tool for planning engineers—it’s a strategic weapon for: If you’re in construction and responsible for delivering on time—this software is for you. FAQs: Everything You Should Know Is construction scheduling analytics software hard to use? Not with Opteam. If you know how to upload a Primavera file or use Excel, you’ll feel right at home. Our platform is built with simplicity in mind. Does it replace my current scheduling tool? No—Opteam enhances it. You still use Primavera or MS Project to build your schedule. Opteam gives you the analytics and visibility those tools lack. What kind of support does Opteam offer? Live support, onboarding assistance, and dedicated chat. You won’t be left guessing. Is it worth the investment? When one missed deadline can cost thousands—or millions—the ROI is crystal clear. 🎯 Let your schedule work for you, not against you. Claim your free Opteam trial Final Thoughts: Delay Is a Data Problem—Solve It with Analytics You wouldn’t drive a car with a blindfold on. So why run a construction project without knowing exactly where your schedule stands? Construction scheduling analytics software turns your timelines from assumptions into action plans. It helps you: And with Opteam, it’s never been easier to get started. ✅ Upload your XER or Excel file.✅ Get your first project dashboard in 2 minutes.✅ No credit card needed. 👉 Start your free trial now
Free Advanced Construction Work Schedule in Excel
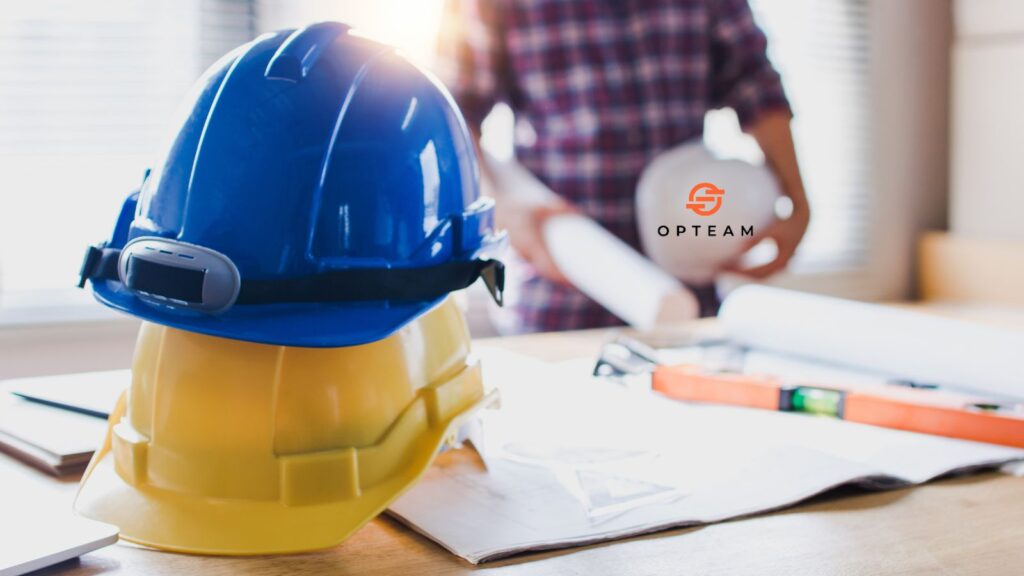
Looking for a ready-to-use, professional construction schedule template? Download our Free Advanced Construction Work Schedule in Excel — built for real projects and real results. Whether you’re a contractor, project manager, or site engineer, this template helps you plan every phase, assign resources, track progress, manage costs, and keep your project on time and on budget. What’s Inside the Free Advanced Construction Work Schedule Excel Template? This Excel file isn’t just a basic task list—it’s a complete construction scheduling system. It includes detailed phases like excavation, foundation, MEP works, and finishing, with start and end dates, durations, team assignments, task dependencies, and buffer days. You’ll also find cost estimates vs. actuals, baseline comparisons, task statuses, and progress tracking. Everything is organized in a clear, editable format that saves you hours of setup time. Why Use an Advanced Construction Schedule Instead of a Basic One? Basic schedules can’t handle the complexity of real construction projects. They often miss dependencies, don’t track progress or costs, and fail to reflect delays. An advanced schedule like this one gives you better control over your timeline, helps you anticipate issues before they become critical, and keeps your team aligned from day one. It’s the difference between reacting to problems and proactively managing them. How to Customize This Free Construction Work Schedule for Your Project The Excel format is fully editable, so you can tailor every task, date, cost, and team assignment to match your specific project. Want to add more trades? Adjust buffer days? Include subcontractor names or Gantt-style visuals? It’s all possible with a few clicks. You can also link it with other planning tools or upload it to your construction management system for real-time collaboration. Download the Free Advanced Construction Work Schedule in Excel Format Ready to simplify your project planning? Click the link below to instantly download your free Excel construction work schedule. No signups or complicated steps—just a powerful tool you can start using today. Perfect for contractors, engineers, and site managers who want better planning without paying for expensive software.
Free XER File Viewer Online – Check the Health of Your P6 Files
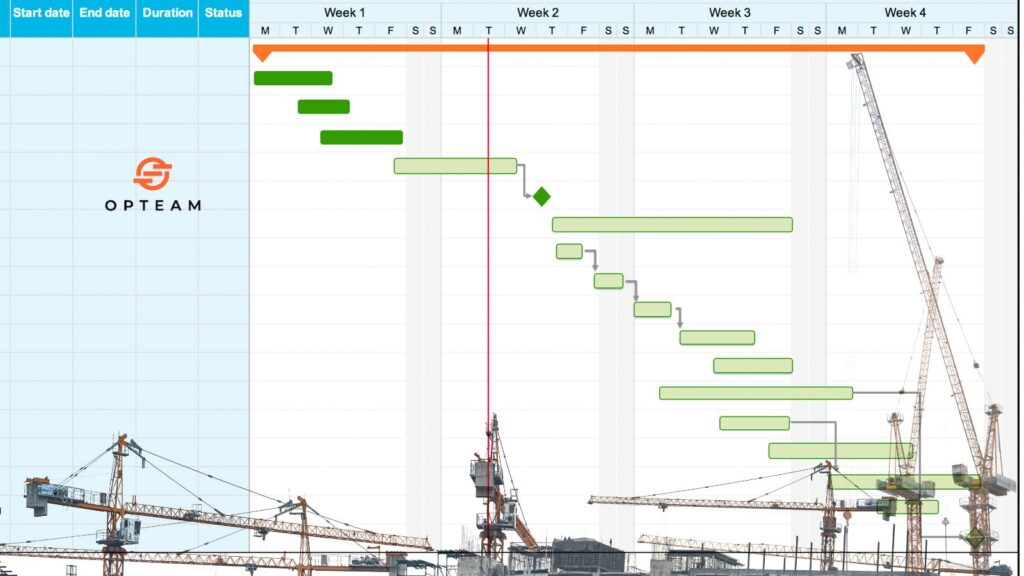
Managing construction schedules in Primavera P6? Don’t risk working with corrupted or poorly structured XER files. Our online XER file viewer helps you quickly inspect file structure, spot red flags, and ensure data integrity. Whether you’re validating subcontractor schedules or auditing baselines, our software gives you instant insights into your project files. Automate progress tracking and schedule analysis beyond just XER file checks. What Is an XER File and Why It Matters in Construction Scheduling? n XER file is the native export format used by Primavera P6, one of the most widely used project scheduling tools in the construction industry. These files contain critical project data—including activities, relationships, calendars, WBS, resources, and more—making them essential for sharing and analyzing schedules across teams. Whether you’re a contractor, consultant, or project owner, understanding what’s inside an XER file helps you assess project health, verify updates from subcontractors, and catch schedule manipulation early. A poorly structured XER file can lead to miscommunication, delay claims, and costly rework. That’s why having a reliable way to inspect XER files—without relying solely on P6—is crucial for maintaining transparency, accountability, and schedule integrity on your projects. Common Issues Found in Poorly Structured XER Files Not all XER files are created equal. When schedules are exported without proper structure or oversight, they can cause more confusion than clarity. Here are some of the most common issues found in poorly structured XER files: Spotting these issues early helps ensure that your project decisions are based on clean, trustworthy data. A free XER file viewer makes this process fast and accessible—even if you don’t have P6 installed. Progress Tracking with Opteam vs. Traditional