Poor Planning in Construction: 5 Killer Consequences
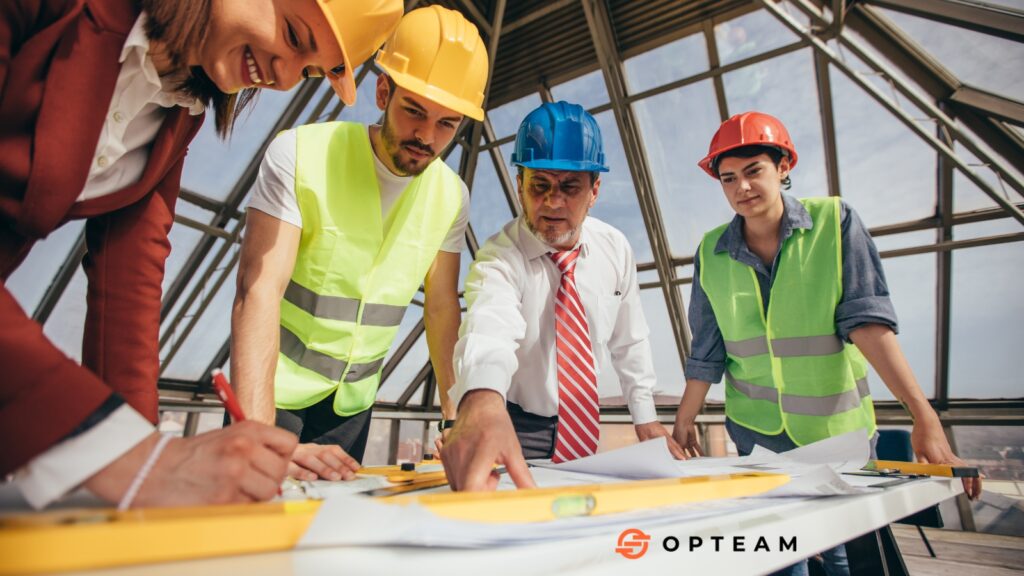
Poor planning in construction can lead to a cascade of issues that can derail even the most promising projects. Imagine pouring time, money, and resources into a project, only to see it crumble under the weight of delays, budget overruns, and safety hazards. It’s a nightmare that no contractor wants to face. But the good news? Avoiding these pitfalls is possible with the right approach to project management. In this article, we’ll explore five killer consequences of poor planning in construction and how to steer clear of them to keep your projects on track. Causes of Poor Planning 1. Lack of Clear Objectives and Scope Without well-defined objectives and a clear project scope, construction projects are set up for failure from the start. This lack of direction leads to confusion among team members, frequent changes in project requirements, and misalignment of expectations. As a result, time and resources are wasted on tasks that don’t contribute to the project’s overall goals, causing delays and cost overruns. 2. Insufficient Risk Assessment Failing to conduct a thorough risk assessment can leave a project vulnerable to unexpected challenges. From unforeseen site conditions to regulatory hurdles, inadequate planning for potential risks results in reactive decision-making that disrupts the project timeline. A comprehensive risk assessment is essential for anticipating potential issues and developing contingency plans that keep the project on track. 3. Poor Communication and Coordination Effective communication and coordination are the backbone of successful construction projects. When communication channels are weak or mismanaged, it leads to misunderstandings, errors, and rework. Poor planning often overlooks the importance of establishing clear lines of communication between stakeholders, contractors, and the project team, leading to fragmented efforts and delays. 4. Inadequate Resource Management Proper planning involves meticulous resource allocation, including labor, materials, and equipment. Inadequate resource management can result in shortages or surpluses, driving up costs and slowing down progress. When resources are not efficiently planned and scheduled, projects may experience bottlenecks or idle time, ultimately affecting the project’s overall performance and profitability. 5. Unrealistic Timelines and Budgeting Setting unrealistic timelines and budgets is a common pitfall in construction planning. Pressure to meet aggressive deadlines or cut costs can lead to rushed planning processes that overlook crucial details. This approach not only increases the likelihood of errors and rework but also strains the entire project team, leading to burnout and decreased productivity. Realistic planning that factors in potential setbacks is key to achieving project success. Consequences 1. Delays and Project Overruns Poor planning in construction can lead to significant delays and project overruns, with studies showing that nearly 70% of construction projects face delays due to inadequate planning and scheduling (source). These delays not only extend the project timeline but also increase costs exponentially, as contractors must account for additional labor, materials, and equipment usage. 2. Increased Costs and Budget Overruns Projects that suffer from poor planning are far more likely to exceed their budgets. In fact, research indicates that almost 75% of projects experience cost overruns, primarily due to poor initial planning and inaccurate cost estimations (source). These overruns can escalate to 20-30% over the original budget, putting a strain on stakeholders and potentially jeopardizing the financial viability of the project. 3. Reduced Quality and Rework Lack of proper planning often results in compromised quality and increased rework, which is costly and time-consuming. Studies show that rework can account for up to 5-20% of total project costs, a direct consequence of insufficient planning, poor communication, and lack of clarity in project scope (source). This not only affects the project’s profitability but also damages the reputation of the construction firm involved. 4. Safety Hazards and Accidents Poor planning is a major contributor to construction site accidents and safety hazards. According to industry data, about 60% of construction accidents can be traced back to inadequate planning and risk assessment (source). These incidents not only result in injuries and fatalities but also lead to significant legal liabilities, project stoppages, and increased insurance costs. 5. Stakeholder Dissatisfaction and Legal Disputes Inefficient planning can lead to unmet expectations, causing dissatisfaction among stakeholders. Approximately 30% of construction projects face disputes and legal challenges, often stemming from issues related to planning failures (source). These disputes can further delay the project, escalate costs, and damage business relationships, highlighting the critical need for meticulous planning from the outset. You had enough with poor planning? Opteam is here to help! Tired of dealing with the costly consequences of poor planning in your construction projects? It doesn’t have to be this way. With Opteam Construction Planning and Scheduling Software, you can take control of your projects like never before. Opteam helps you set clear objectives, manage resources efficiently, and maintain realistic timelines, all while keeping your team on the same page. Say goodbye to delays, budget overruns, and rework—Opteam’s advanced analytics and user-friendly interface make it easy to plan ahead and avoid the pitfalls that plague so many construction projects. Plus, with built-in risk assessment tools, you can identify and mitigate potential issues before they become costly problems. Ready to see how Opteam can transform your project planning? Book a free demo today and try the system free for 14 days. Don’t let poor planning hold you back—take the first step towards smarter, more efficient construction management with Opteam! Bid Farewell to delays & cost overruns Book your demo now & Try Opteam Construction Planning & Scheduling Software Free for 14 days, No strings attached! I’m In
Construction Management Vs Project Management: Key Differences
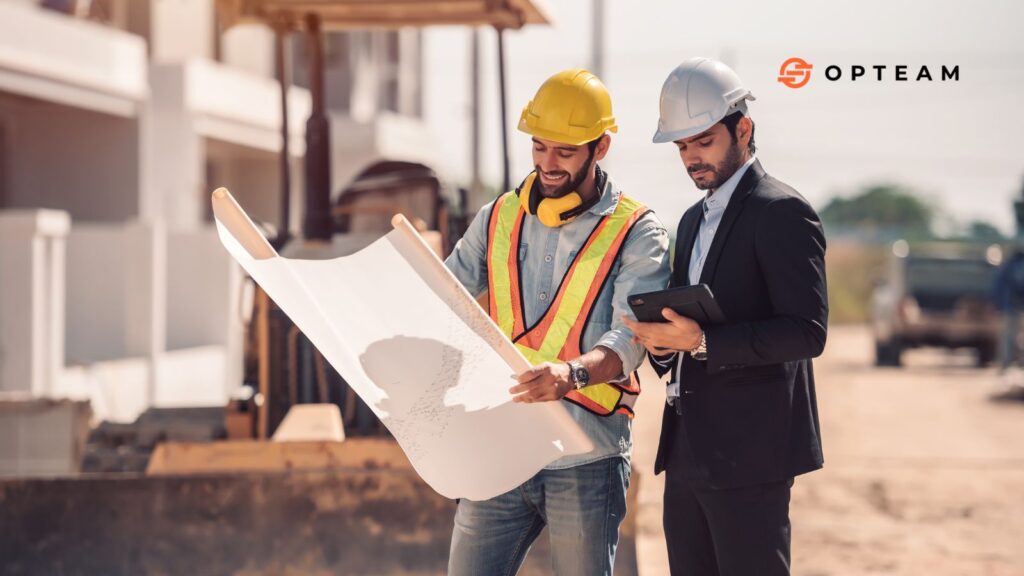
Are you losing sleep over project delays, cost overruns, or miscommunications on the job site? The construction industry is full of challenges, and the confusion between construction management and project management could be making things worse. It’s easy to blur the lines, but this mix-up might be dragging your projects down. Imagine a critical task slipping through the cracks because roles weren’t clear—or worse, your project going over budget because of misunderstood responsibilities. The stress of managing construction projects is already high, so why add more pressure by not knowing who’s truly in charge of what? This lack of clarity can lead to costly mistakes, missed deadlines, and a whole lot of frustration. Before your next project hits a roadblock, let’s break down the key differences between construction management and project management. Understanding these distinctions could be the game-changer you need to keep your projects on track and your stress levels in check. What is construction management? Construction management is a professional service that involves the overall planning, coordination, and control of a construction project from beginning to end. It encompasses a broad range of activities that are aimed at ensuring the successful delivery of a project, whether it’s a residential building, a commercial complex, or a large infrastructure project. Unlike traditional construction roles that might focus on specific aspects like design or labor, construction management integrates all elements of the construction process, bringing together various disciplines to work towards a common goal. At its core, construction management is about translating a project’s vision into reality. It involves a strategic approach to managing the entire construction process, from initial concept and design to the final touches. What is project management? Project management is a structured approach to planning, executing, and completing projects across various industries, including construction, IT, finance, and more. It involves applying knowledge, skills, tools, and techniques to meet specific project goals and deliverables within defined constraints like scope, time, cost, and quality. Project management is not confined to a particular sector or type of work; instead, it’s a versatile framework used to guide projects from conception through to completion, ensuring that the project meets its objectives and satisfies stakeholders. At its essence, project management is about turning ideas into actionable plans and ensuring those plans are carried out effectively. It provides a roadmap for managing resources, time, and risk, while aligning team efforts towards common goals. Project management methodologies, such as Agile, Waterfall, or Lean, offer structured ways to approach different types of projects, making it adaptable to diverse project requirements. Construction Management Vs Project Management Responsibilities When comparing construction management and project management within the construction industry, their responsibilities, though closely related, cater to different aspects of the project lifecycle. Construction management is deeply rooted in the hands-on, on-site execution of the project. It focuses on the day-to-day operations of the construction phase, including managing the construction crew, overseeing subcontractors, and ensuring that the work is carried out according to the design specifications and safety standards. Construction managers are responsible for the direct control of the construction activities, making real-time decisions to address site issues and adjust schedules as needed to keep the project on track. On the other hand, project management in construction is a broader discipline that encompasses the entire project from inception to completion. A project manager’s responsibilities start earlier and extend further, involving the initial planning stages, defining the project scope, setting objectives, and managing overall project timelines and budgets. They coordinate with all stakeholders, including clients, architects, engineers, and the construction management team, to ensure that the project aligns with the agreed-upon goals and constraints. Project managers are also tasked with risk management, quality assurance, and maintaining communication among all parties to ensure that the project stays aligned with the client’s vision. While construction managers focus on the technical and operational aspects on-site, project managers take a more strategic role, overseeing the big picture to ensure that all elements of the project fit together smoothly. Decision-Making Authority In construction projects, decision-making authority differs significantly between construction management and project management. Construction managers have authority over on-site decisions related to daily operations, such as resource allocation, work sequencing, and immediate problem-solving. They make real-time decisions that directly impact the construction process, focusing on keeping the project on schedule and ensuring quality and safety standards. Project managers, however, have a broader decision-making scope that spans the entire project lifecycle. They make strategic decisions about project direction, scope adjustments, major budget allocations, and overall timelines. While they do consider on-site inputs from construction managers, project managers are primarily responsible for high-level decisions that align the project with its overarching goals, stakeholder expectations, and long-term objectives. Communication and Coordination In construction, construction managers focus on on-site communication, coordinating with subcontractors and workers to keep daily operations running smoothly. They handle immediate on-site issues and ensure that tasks are clearly understood and executed. Project managers, however, oversee broader communication, liaising with all stakeholders, including clients, architects, and engineers. They coordinate across different teams to align project phases and ensure everyone is on the same page regarding project goals, progress, and any changes needed. Other areas Aspect Construction Management Project Management Scope of Work Focuses on on-site execution and operational details. Manages the overall project lifecycle and strategic planning. Risk Management Deals with immediate, on-site risks and issues. Manages overall project risks and strategic adjustments. Budget Management Oversees on-site costs and resource management. Handles overall project budgeting and financial planning. Quality Control Ensures construction work meets design and safety standards. Assures that project goals and quality standards are met. Time Management and Scheduling Manages daily schedules and on-site timelines. Oversees overall project timelines and major milestones. Resource Management Manages on-site labor, equipment, and materials. Allocates and monitors resources across the entire project. Compliance and Regulations Ensures adherence to site-specific safety and building codes. Ensures compliance with overall project regulations and standards. Tools and Technology Utilizes tools specific to construction operations. Uses project management software and methodologies.
Cost Value Reconciliation (CVR) in Construction: Your Full Guide
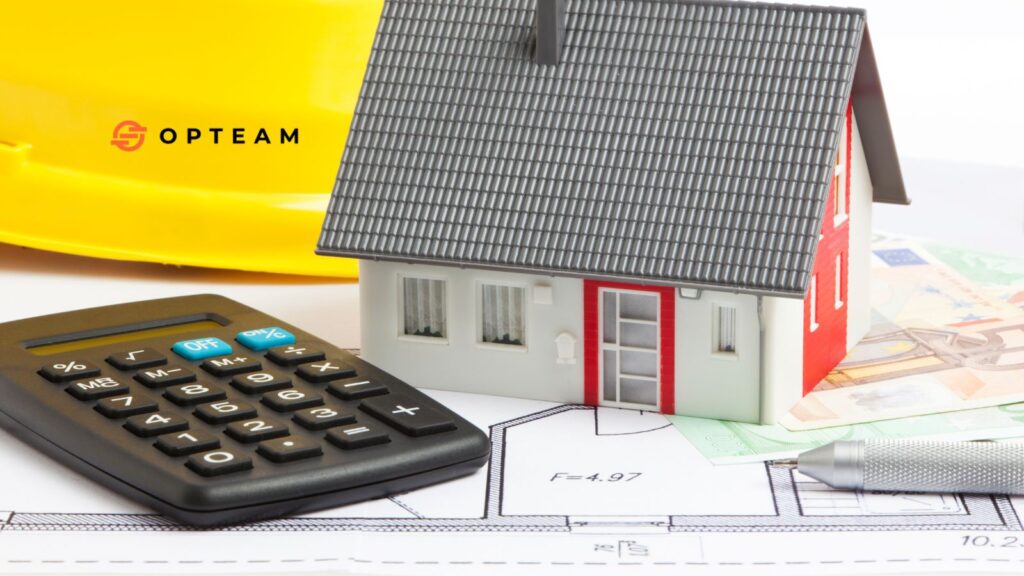
Cost Value Reconciliation (CVR) is a financial management process used in construction to compare the actual costs incurred on a project with the value of work completed. This process helps to determine the profitability of a project by providing a clear snapshot of whether the project is making or losing money at any given time. CVR involves analyzing various cost elements, such as labor, materials, and overheads, and matching them against the revenue generated from the work done. The primary purpose of CVR is to maintain control over project finances by identifying variances between expected and actual costs. Why CVR is needed in construction? Cost Value Reconciliation (CVR) is essential in construction because it provides a clear financial oversight of a project, ensuring that costs are controlled and managed effectively. In the complex and dynamic environment of construction, where costs can quickly spiral due to unexpected changes, delays, or mismanagement, CVR acts as a safeguard. By regularly comparing the actual costs with the value of work completed, CVR helps identify discrepancies early, allowing project managers to take corrective measures before financial problems escalate. This proactive approach not only prevents budget overruns but also enhances the overall financial stability of the project. Another critical reason for the need for CVR in construction is its role in improving profitability and cash flow management. Through CVR, construction firms can accurately assess their financial performance, making it easier to forecast future cash needs and manage resources more efficiently. It helps in identifying areas where costs are exceeding planned budgets, providing a basis for renegotiations, cost-cutting, or adjustments in project execution. This leads to better-informed decision-making and ensures that the project remains financially viable from start to finish. Additionally, CVR fosters transparency and accountability within the project team and stakeholders. By regularly reporting on the financial status of a project, CVR builds trust and confidence among clients, investors, and other stakeholders, as it demonstrates a commitment to financial discipline and responsible project management. It serves as a critical tool for aligning all parties involved, helping to set realistic expectations and manage financial risks effectively. This alignment ultimately contributes to the successful delivery of construction projects on time and within budget. Who & When? The responsibility for conducting Cost Value Reconciliation (CVR) typically falls on the project management and finance teams within a construction company. Key roles involved include: Commercial Manager: Uses CVR to assess project profitability and ensure that financial targets are met. They are involved in strategic decision-making based on the outcomes of the CVR. Project Manager: Oversees the overall financial health of the project and uses CVR data to make informed decisions about managing costs and resources. Quantity Surveyor: Plays a crucial role in the CVR process by measuring and valuing the work completed. They are responsible for tracking costs, valuing variations, and preparing reports that feed into the CVR analysis. Financial Controller or Accountant: Supports the CVR process by ensuring that all financial data is accurate and up-to-date. They provide insights into cash flow, revenue recognition, and overall financial performance. CVR is conducted regularly throughout the life cycle of a construction project. The frequency depends on the project size, complexity, and specific contractual or company requirements, but it is commonly done: Regular CVR reporting helps ensure that any financial issues are identified and addressed promptly, maintaining the project’s financial integrity throughout its duration. Cost Value Reconciliation Format The Cost Value Reconciliation (CVR) format typically includes several key sections that provide a comprehensive overview of a project’s financial status. Here’s a basic outline of a typical CVR format: 1. Project Information 2. Summary Section 3. Detailed Cost Analysis 4. Revenue Analysis 5. Cash Flow Analysis 6. Forecasting 7. Comments/Notes 8. Sign-offs This format ensures a comprehensive review of the financial performance of the project, allowing for effective monitoring, control, and decision-making.
Construction Scheduling Oversight: Full Guide
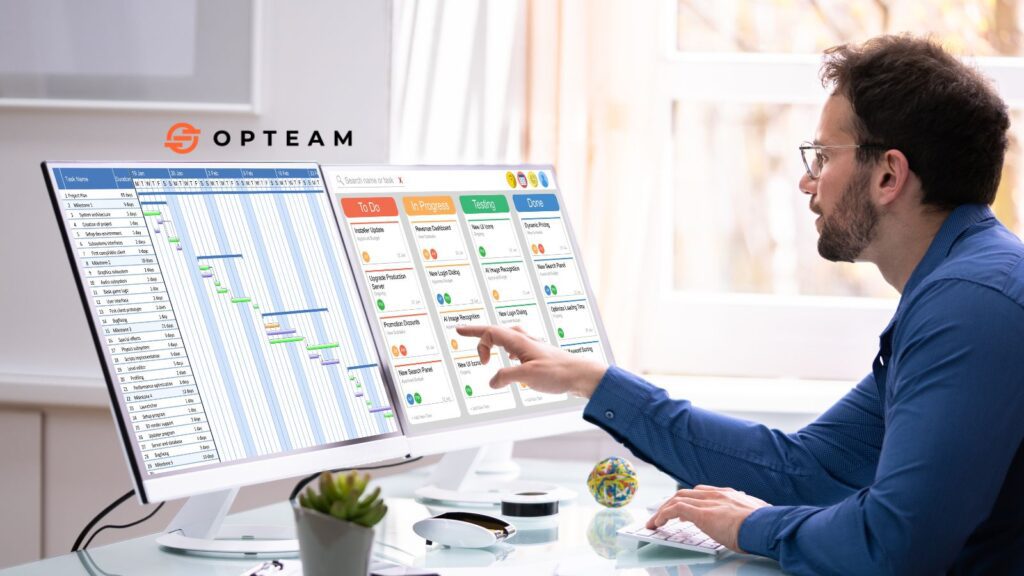
Construction Scheduling Oversight refers to the process of monitoring, reviewing, and managing the construction schedule to ensure that a project stays on track, meets deadlines, and adheres to budget constraints. This oversight involves regular updates, adjustments, and the identification of potential delays or issues that could impact the project’s timeline. The goal is to ensure that all phases of the construction process are aligned with the planned schedule, minimizing risks and improving overall project efficiency. Process 1- Reviewing Schedules Reviewing schedules in construction is a critical step in ensuring a project’s success. It involves a thorough examination of the proposed timeline to confirm that all tasks, milestones, and deadlines are realistic and achievable. This process requires a deep understanding of the project’s scope, resources, and potential challenges. By carefully reviewing the schedule, project managers can identify any unrealistic timeframes, sequencing issues, or resource constraints that could lead to delays or budget overruns. It also provides an opportunity to align the schedule with the project team’s capabilities and any external factors, such as weather conditions or material availability. 2- Tracking Progress Tracking progress in construction is essential for ensuring that a project stays on course and meets its deadlines. It involves continuously monitoring the actual progress of construction activities against the planned schedule to identify any deviations or delays. Effective progress tracking allows project managers to quickly spot potential issues, such as tasks falling behind or resource shortages, and take corrective actions before these issues escalate. Opteam, our cutting-edge progress tracking software, takes this process to the next level by providing real-time data and insights. With Opteam, project managers can easily compare actual progress with the planned schedule, visualize critical paths, and assess the impact of any delays or changes. The software’s intuitive interface and advanced analytics make it easier to identify bottlenecks and allocate resources more efficiently. By automating much of the tracking process, Opteam reduces the risk of human error and ensures that all stakeholders have access to up-to-date information, enabling quicker, more informed decision-making. This proactive approach to progress tracking helps keep projects on track, ensuring timely and cost-effective completion. 3- Identifying Issues Identifying issues in construction scheduling is crucial for preventing delays and cost overruns. This process involves closely monitoring the project timeline and activities to spot potential problems early, such as resource shortages, sequencing conflicts, or unexpected delays. By catching these issues before they escalate, project managers can implement solutions quickly, whether by adjusting the schedule, reallocating resources, or addressing the root cause. Proactively identifying and resolving issues not only keeps the project on track but also minimizes disruptions, ensuring smoother execution and a higher likelihood of meeting project deadlines and budgets. 4- Making Adjustments Making adjustments in construction scheduling is a dynamic process that ensures the project remains on track despite any unforeseen challenges. When issues or delays are identified, it’s essential to revisit the schedule and make necessary changes to accommodate these developments. This might involve re-sequencing tasks, reallocating resources, or extending deadlines to ensure that the overall project timeline is still achievable. Adjustments are often needed due to factors like weather disruptions, material shortages, or changes in project scope. By being flexible and responsive in making these adjustments, project managers can maintain momentum and prevent small setbacks from snowballing into larger problems. This adaptability is key to delivering a successful project that meets both time and budget expectations. 5- Reporting Reporting in construction scheduling is the process of keeping all stakeholders informed about the project’s progress, challenges, and any adjustments made to the schedule. Regular and transparent reporting ensures that everyone involved, from project managers to clients, is aware of the current status of the project and any potential risks or delays. Effective reporting involves sharing key metrics, such as completed tasks, upcoming milestones, and any deviations from the original plan. It also includes providing insights into how any identified issues are being addressed and the impact of these actions on the overall timeline. By maintaining clear and consistent communication through reporting, trust is built among stakeholders, and any concerns can be addressed promptly, ensuring that the project continues smoothly toward successful completion. Final Words In conclusion, construction scheduling oversight is a critical component of any successful project. By diligently reviewing schedules, tracking progress, identifying issues, making timely adjustments, and maintaining clear reporting, you can ensure that your construction projects stay on track and within budget. Implementing these practices not only mitigates risks but also enhances efficiency and communication among all stakeholders. Stay proactive, stay informed, and lead your projects to success with comprehensive oversight.
The Basics of Cost Reporting in Construction
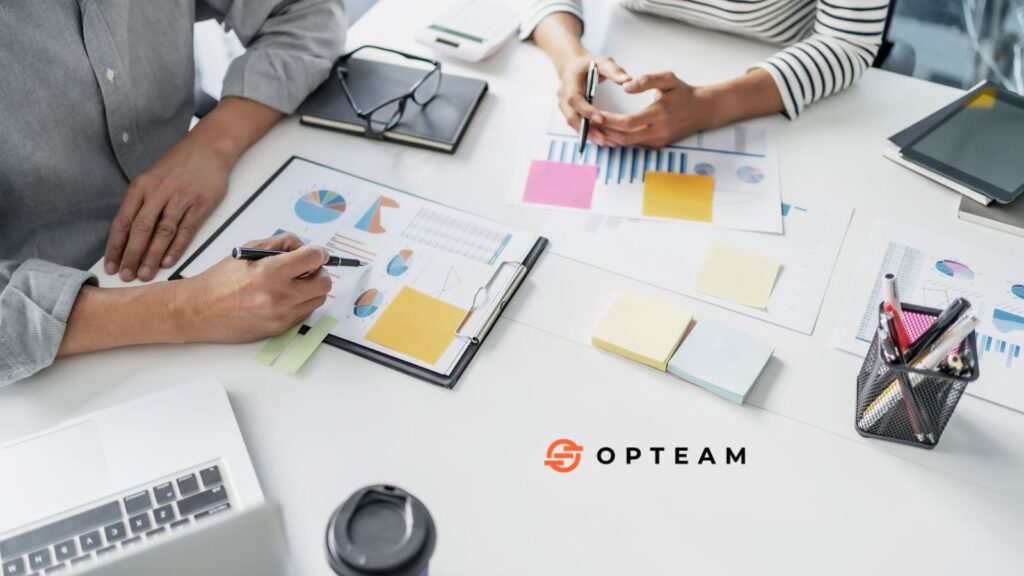
Cost reporting in construction can often feel like a daunting task, fraught with complexities that lead to inaccuracies and inefficiencies. Without effective cost reporting, project managers face unpredictable expenses, budget overruns, and financial strain that can jeopardize the success of their projects. The lack of clarity in financial tracking makes it challenging to maintain control over project costs, potentially leading to costly delays and mismanagement. Harnessing advanced cost reporting tools in construction can transform how you manage your projects, offering precise insights and streamlined financial tracking. By adopting effective cost reporting practices, you can ensure that your projects stay within budget, minimize financial risks, and enhance overall project efficiency. Ready to learn how? Continue reading to discover practical strategies and solutions for mastering cost reporting and keeping your projects on track. What is Cost Reporting in Construction? Cost reporting in construction is the process of documenting and analyzing all financial aspects of a construction project. This includes tracking expenses such as labor, materials, equipment, and subcontractor costs to ensure they align with the project’s budget. Effective cost reporting provides a clear picture of where money is being spent, identifies potential financial issues early, and helps in making informed decisions to control costs and manage resources efficiently. In addition to tracking actual costs, cost reporting often involves forecasting future expenses and comparing them against the project’s budgeted figures. This allows project managers to identify variances, understand the reasons behind them, and take corrective actions as needed. Accurate and timely cost reporting is crucial for maintaining financial control, ensuring project profitability, and delivering successful outcomes within the allocated budget. Different Types of Costs in Construction Projects Cost Type Description Direct Costs Costs directly associated with the construction work, such as materials, labor, and equipment. Indirect Costs Costs not directly tied to specific tasks but necessary for the project, like utilities, administrative expenses, and insurance. Fixed Costs Costs that do not change with the level of work performed, such as project management salaries and site overhead. Variable Costs Costs that fluctuate based on project activity, including materials and subcontractor fees. Contingency Costs Funds set aside for unexpected expenses or risks that may arise during the project. Overhead Costs General expenses required to support the project but not directly attributed to specific tasks, such as office rent and utilities. Common Challenges with Construction Cost Reporting Here are some common challenges with cost reporting in construction: How Technology Helped Tackling These Challenges Technology has significantly improved the accuracy of cost reporting in construction by automating data entry and reducing human error. Modern software solutions allow for real-time tracking of expenses, ensuring that all costs are recorded correctly and consistently. This automation helps project managers maintain accurate financial records, minimizing the risk of discrepancies and ensuring that reports reflect the true financial state of the project. In addition to improving accuracy, technology has also addressed the challenge of delayed reporting. With cloud-based platforms and mobile applications, project teams can input and access cost data instantly from any location. This real-time access allows for more frequent and timely updates, enabling project managers to make informed decisions quickly. By integrating cost reporting tools with other project management systems, technology ensures that all relevant data is consolidated in one place, streamlining the reporting process and reducing the likelihood of incomplete or outdated information. Furthermore, technology has enhanced communication and collaboration between different departments involved in construction projects. Integrated software solutions facilitate the sharing of cost data between project managers, accountants, and other stakeholders, ensuring that everyone is on the same page. Advanced forecasting and budgeting tools also allow for better anticipation of unforeseen expenses and potential budget variances, helping teams to prepare for and manage these challenges effectively. Overall, the use of technology in cost reporting has led to more efficient, transparent, and accurate financial management in construction projects. Track Your Construction Project with Opteam Tracking your construction project has never been easier with Opteam. Our software provides real-time insights into every aspect of your project, from costs to progress, ensuring you stay on budget and on schedule. With Opteam, you can monitor expenses, forecast potential risks, and make informed decisions quickly, all from one intuitive platform. Streamline your project management and achieve better results in your projects. Read more:
Soft Cost in Construction Explained
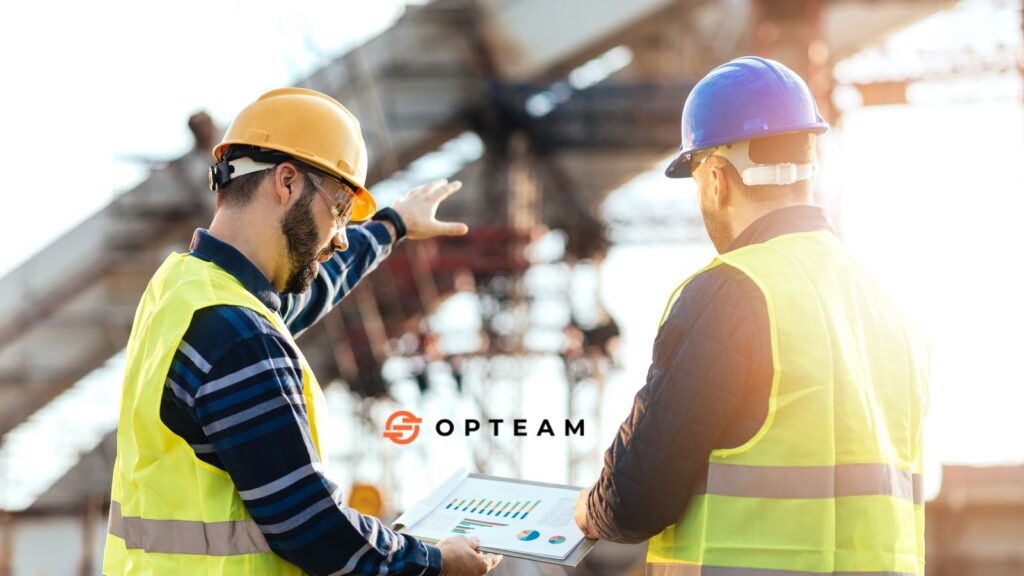
Understanding soft cost in construction is essential for anyone involved in building projects. These costs, often overlooked, encompass everything from design fees to permits and inspections. While they may not be as visible as materials or labor, they play a crucial role in determining the overall budget and success of a project. In this article, we’ll break down what soft costs are, why they matter, and how to manage them effectively. What is soft cost in construction? Imagine you’re about to build your dream home. You’ve planned out every detail, from the materials to the labor, and you think you’ve covered all the expenses. But then, the architect’s bill arrives, followed by fees for permits, insurance, and legal services. These are soft costs in construction—the often-hidden expenses that don’t directly relate to the physical building but are crucial to making the project a reality. Picture this: you’re in a meeting with your project manager, and they’re talking about how to keep the project on track. They mention costs like design fees, project management salaries, and even marketing expenses for commercial projects. These are all soft costs. They might not be as tangible as the bricks and mortar, but without them, the project wouldn’t go from paper to reality. Soft costs ensure that everything behind the scenes runs smoothly, from planning to execution, making them just as vital as the visible parts of your construction budget. Why Soft Costs Are Just as Important as Hard Costs Many people overlook soft costs in construction, focusing primarily on the tangible aspects like materials and labor. This oversight can lead to budget surprises and delays, impacting the overall success of the project. Imagine investing all your resources into building your dream project, only to be blindsided by unexpected expenses like design fees, permits, and legal services. These soft costs might seem secondary, but they are essential for turning your vision into reality. Ignoring them could mean facing unplanned financial strain, stalling your project, or even compromising on quality. By giving soft costs the attention they deserve, you can create a comprehensive budget that accounts for every aspect of your construction project. Properly estimating and managing these costs ensures a smoother process, fewer surprises, and a final product that meets both your expectations and financial plan. How to Accurately Estimate Soft Costs for Your Project 1. Identify All Potential Soft Costs: Start by listing all the non-physical expenses your project might incur, such as design fees, permits, legal services, insurance, and project management. 2. Research Costs: Gather information on the average costs for each item on your list. This can involve contacting professionals, reviewing past projects, or checking industry standards. 3. Consult Experts: Speak with architects, construction companies, engineers, and project managers to get accurate estimates for their services. They can provide insights into any additional soft costs you might have missed. 4. Include Contingency: Add a contingency amount to cover unexpected soft costs. A typical recommendation is to allocate 10-20% of your total budget for this purpose. 5. Regularly Review and Adjust: As your project progresses, revisit your estimates and adjust them as needed. Staying flexible helps you account for any changes or new expenses that arise. Say good bye to cost overruns with Opteam Managing a construction project can feel like trying to balance a budget on a tightrope. Unexpected costs, hidden expenses, and mismanaged funds can easily tip you into financial trouble. But with Opteam, you can keep your budget in check, every step of the way. Opteam is the all-in-one construction planning and scheduling software designed to keep your costs under control. Here’s how: With Opteam, you’re not just managing costs—you’re securing your project’s financial success. Keep your construction projects financially sound with the software that’s built to manage the complexities of budgeting. Final words Understanding and managing soft cost in construction is key to the success of any building project. Through accurately estimating and keeping track of these often-overlooked expenses, you can ensure that your project stays on budget and progresses smoothly. Remember, while they may not be as visible as hard costs, soft costs are essential to turning your construction vision into reality. Plan wisely, manage diligently, and your project will be well on its way to success. Read more:
Extension of Time (EOT) in Construction: Meaning, Full Form, Delays & Claims

In short: EOT stands for Extension of Time, a clause in most construction contracts that allows the project’s completion date to be extended due to delays beyond the contractor’s control. The goal? To protect contractors from penalties when delays aren’t their fault—like adverse weather, regulatory issues, or late approvals. If a project runs late due to reasons outside a contractor’s control, an EOT ensures they’re not hit with liquidated damages unfairly. EOT Full Form & Meaning The full form of EOT is Extension of Time. It’s a formal process that helps project stakeholders adjust the completion date and maintain transparency in case of valid delays. Why Is an EOT Clause Important? EOT provisions: Without an EOT clause, contractors risk being penalized for delays they didn’t cause. Common Reasons for Extension of Time in Construction Here are typical causes that justify EOT claims: How to Apply for an EOT Claim Delay Analysis Methods Used in EOT Claims When preparing an EOT claim, you’ll likely use one of the following delay analysis techniques: Choosing the right delay analysis method is crucial—especially if disputes escalate. What Is a Concurrent Delay? A concurrent delay happens when both the contractor and employer contribute to the delay at the same time. In such cases: This is one of the most debated areas in construction claims and should be addressed clearly in contract terms. Legal Considerations of EOT Claims EOT claims often lead to disputes. Here are legal points to consider: A strong legal framework and clear documentation help avoid conflict. Best Practices for Writing EOT Claims Want to write an EOT that gets approved? Follow these tips: Impact of EOT on Project Timeline and Budget EOTs directly affect project delivery: However, EOT doesn’t automatically mean financial compensation—unless stated in the contract. Stay on Track with Opteam Managing a construction project can be like trying to navigate a ship through unpredictable waters. Delays, miscommunications, and scheduling issues can easily throw you off course. But with Opteam, you can stay on track, every step of the way. Opteam is the all-in-one construction software designed to keep your projects moving forward. Here’s how: With Opteam, you’re not just managing a project—you’re ensuring its success. Keep your construction projects on track with the software that’s built to handle the complexities of the job. Let Opteam be your trusted partner in delivering projects on time, every time Create your free account now & experience its benefits first hand.
Performance Measurement Baseline: How to Plan it?
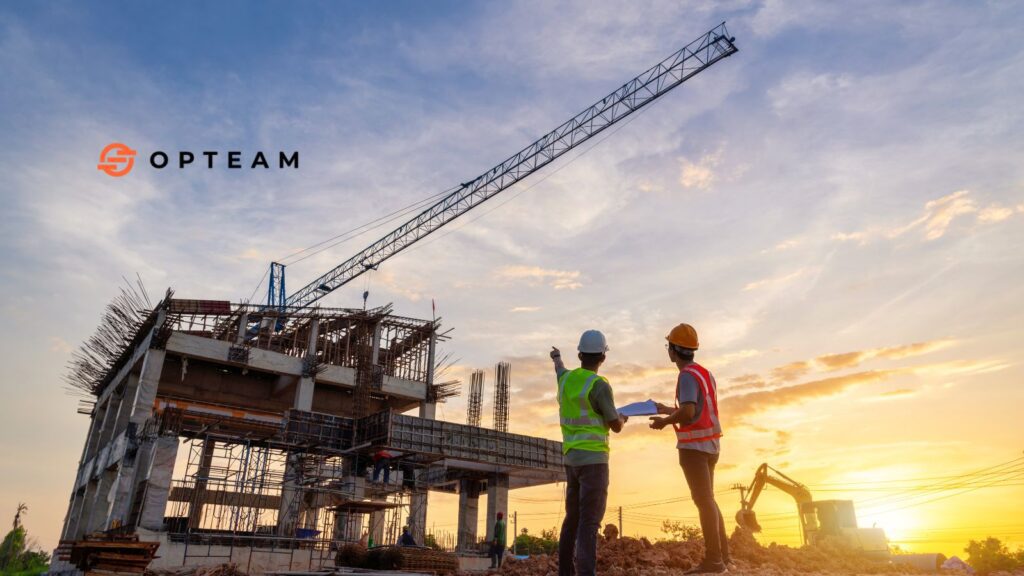
Ever wondered how to keep a project on track from start to finish? That’s where the Performance Measurement Baseline (PMB) comes in. A PMB is like the project’s GPS, guiding you with a solid plan for scope, schedule, and cost. It’s crucial for staying on track and making sure your project meets its goals. In this article, I’ll break down what a PMB is and why it’s essential. By the end, you’ll understand how to set up a PMB and use it to keep your projects on course. The Concept of Performance Measurement Baseline Performance measurement in project management has come a long way. Before tools and software, tracking progress was manual and often inaccurate. The concept of the PMB evolved to bring consistency and reliability to project management. Components of PMB A PMB has three main components: 1- Scope Baseline: Defines what’s included in the project and helps avoiding scope creep. 2- Schedule Baseline: Outlines the project timeline & keeps the project on schedule. 3- Cost Baseline: Estimates the budget & tracks spending against the plan. Relationship with Project Plan Think of the PMB as the backbone of your project plan. It integrates with the overall project plan, ensuring everything aligns with the project’s goals. This alignment helps in making informed decisions and controlling the project effectively. Setting Up a Performance Measurement Baseline Initial Planning Start by identifying your project objectives and deliverables. Set clear, measurable criteria for performance. Ask yourself: Developing the Baselines Scope Baseline: Create a Work Breakdown Structure (WBS) & clearly define all the tasks and deliverables. Schedule Baseline: Develop a detailed project schedule & use Gantt charts or project management software to map out the timeline. Cost Baseline: Estimate project costs accurately & allocate budget to each task and phase. Tools and Techniques Use project management software like MS Project, Primavera or Opteam. These tools help in setting up and maintaining baselines. Analytical techniques, like Earned Value Management (EVM), are also handy for tracking performance. Benefits of a Performance Measurement Baseline Enhanced Project Control A PMB allows you to monitor and track project progress. You can identify variances early and take corrective actions. Improved Communication With a PMB, communication among stakeholders becomes clear and effective. It provides a common reference point for all performance-related discussions. Risk Management A PMB helps in the early identification of potential risks. You can proactively manage and mitigate these risks, ensuring smoother project execution. Challenges in Establishing and Maintaining a PMB Common Obstacles Setting up a PMB isn’t always smooth sailing. Some common challenges include: Strategies to Overcome Challenges Here’s how to tackle these obstacles: Future Trends in Performance Measurement Baseline Conclusion A Performance Measurement Baseline is essential for successful project management. It enhances control, improves communication, and helps manage risks. Adopting a PMB can significantly improve your project outcomes. Continuously refine your PMB processes for better results. References Books and Articles Online Resources FAQs Q: What is a Performance Measurement Baseline?A: It’s a plan for scope, schedule, and cost used to measure project performance. Q: Why is a PMB important?A: It helps in tracking progress, managing risks, and ensuring the project stays on track. Q: How do you set up a PMB?A: Identify project objectives, develop detailed baselines for scope, schedule, and cost, and use project management tools. Q: What challenges might I face with a PMB?A: Common challenges include resistance to change, inaccurate estimates, and lack of stakeholder engagement. Use these tips and insights to leverage your Performance Measurement Baseline for better project management.
Comprehensive Guide to Construction Delay Analysis
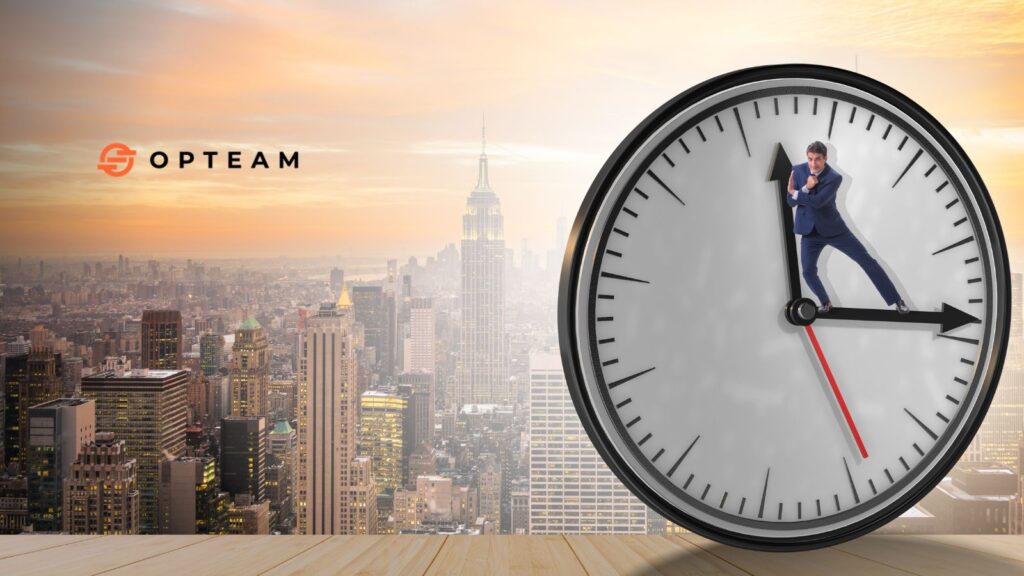
Construction delays can wreak havoc on project timelines, inflate budgets, and strain client relationships. These setbacks are not just minor inconveniences; they can significantly impact the overall success and profitability of a project.Imagine investing months of hard work and resources into a project, only to have unforeseen delays push the completion date back by weeks or even months. The frustration of navigating the complexities of delay causes, legal implications, and cost overruns can be overwhelming. Without a solid understanding of delay analysis, these challenges can become insurmountable obstacles. In this comprehensive guide to construction delay analysis, we will explore proven strategies, essential tools, and innovative solutions to help you effectively manage and mitigate delays. By mastering the art of delay analysis, you can ensure your projects stay on track, within budget, and maintain strong client satisfaction. What is Delay Analysis in Construction? Delay analysis in construction is a systematic process used to determine the reasons, impacts, and responsibilities for delays in a construction project. This analysis helps project managers, contractors, and stakeholders understand how delays have affected the project timeline and identify measures to mitigate future delays. The primary goals of delay analysis are to: Types of Delay Analysis in Construction As-Planned vs. As-Built Analysis As-Planned vs. As-Built Analysis is a fundamental method used in construction delay analysis to compare the project’s initial schedule (as-planned) with the actual progress made (as-built). This analysis helps in identifying discrepancies between what was originally intended and what actually occurred during the project. By mapping out the planned activities against the actual timeline, stakeholders can clearly see where delays happened, the duration of these delays, and how they impacted the overall project schedule. This type of analysis is invaluable for pinpointing specific areas where delays occurred and understanding their causes. For example, if certain tasks took longer than expected, the analysis can reveal whether the delays were due to internal inefficiencies, such as inadequate resource allocation, or external factors like unexpected weather conditions. The As-Planned vs. As-Built Analysis is widely used in construction project management due to its straightforward approach and effectiveness in highlighting deviations from the original schedule. It provides a clear visual representation of the project’s progress, making it easier for stakeholders to communicate about delays and their impacts. Moreover, this analysis supports the development of more accurate future project schedules by learning from past discrepancies. It also strengthens project control mechanisms, ensuring that potential delays are identified and addressed promptly, thereby enhancing the likelihood of on-time project completion and better resource management. Impacted As-Planned Analysis Impacted As-Planned Analysis is a delay analysis method that involves modifying the original project schedule by incorporating the delays as they occurred to assess their impact on the overall timeline. This approach helps project managers understand how each delay event affects the project completion date by sequentially adding the delays to the as-planned schedule. By doing so, it highlights the cumulative effect of all delays, offering a clear view of their impact on the project’s progress. This type of analysis is particularly useful for identifying and demonstrating the direct consequences of specific delays, whether caused by the client, contractor, or unforeseen circumstances. It allows stakeholders to visualize the ripple effect of each delay, showing how initial setbacks can cascade through subsequent activities, leading to significant shifts in the project schedule. Collapsed As-Built (But-For) Analysis Collapsed As-Built (But-For) Analysis involves removing delays from the actual project schedule to determine what the completion date would have been without those delays. This method provides a hypothetical scenario to show how the project could have progressed if no delays had occurred, helping to identify the specific impact of each delay and clarify responsibility. Window Analysis Window Analysis divides the project timeline into smaller time segments or “windows” to evaluate delays within each period. By analyzing delays in these shorter intervals, this method offers a more detailed and granular understanding of how delays affected the project over time, allowing for more precise identification and resolution of delay issues. Time Impact Analysis (TIA) Time Impact Analysis (TIA) assesses the impact of delays on the project schedule at the time they occur. It involves inserting delay events into the project schedule as they happen and evaluating their effects on the overall timeline. This proactive approach helps in managing ongoing projects by continuously updating and understanding the schedule’s evolving impact. Earned Value Management (EVM) Analysis Earned Value Management (EVM) Analysis uses project performance metrics to evaluate schedule and cost variances. By comparing the planned value of work with the actual value earned and the actual cost incurred, EVM provides insights into project performance, allowing managers to identify delays and forecast future performance more accurately. Fragnets (Fragmentary Networks) Fragnets (Fragmentary Networks) involve breaking down the project schedule into smaller sections or fragments to analyze specific delays. This method focuses on particular activities or sequences of activities, offering a detailed view of how delays in one part of the project affect the overall timeline. It is useful for identifying and addressing localized delay issues. How to avoid delays? Tip Description Effective Planning Develop a detailed project plan with clear timelines, milestones, and contingency plans. Clear Communication Maintain open and regular communication among all stakeholders to ensure everyone is aligned. Resource Management Ensure that all necessary resources, including materials and labor, are available when needed. Regular Progress Monitoring Continuously monitor project progress against the plan to identify and address issues early. Risk Management Identify potential risks early and develop mitigation strategies to prevent delays. Stakeholder Coordination Coordinate with all parties involved, including contractors, suppliers, and clients, to avoid conflicts. Efficient Decision Making Make timely decisions to avoid bottlenecks and keep the project moving forward. Quality Control Implement strict quality control measures to avoid rework and associated delays. Use of Technology Utilize project management software and other technologies to improve efficiency and tracking. Regular Site Inspections Conduct frequent site inspections to ensure work is progressing as planned and identify issues early. Tackle Delays Before They Happen with
SWAG Meaning in Construction: From A to Z
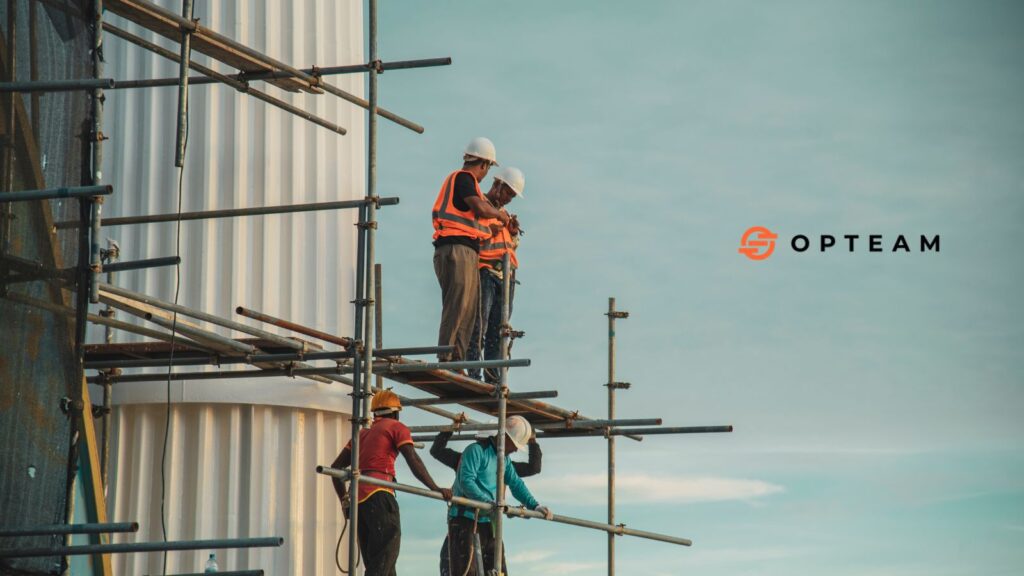
In the construction industry, the acronym SWAG stands for “Scientific Wild-Ass Guess.” It is a term used to describe an educated guess based on experience, intuition, and available data when precise information is lacking. While it may sound informal, a SWAG is often employed during the early stages of a project when there is insufficient detailed information to make accurate calculations. This approach allows project managers and engineers to estimate costs, timelines, and resource requirements with a reasonable degree of confidence, helping to set initial expectations and guide decision-making. SWAGs play a crucial role in the planning and budgeting phases of construction projects. When detailed plans and specifications are not yet available, project stakeholders rely on SWAGs to create preliminary budgets and schedules. These estimates are typically refined as more information becomes available and as the project progresses. By using a SWAG, project teams can move forward with a project even when faced with uncertainties, ensuring that progress is not stalled due to a lack of detailed data. Practical Applications 1. Preliminary Cost Estimation 2. Project Scheduling 3. Resource Allocation 4. Risk Management 5. Client Communication 6. Innovation and Problem-Solving How is the Swag Estimate Determined? The determination of a SWAG (Scientific Wild-Ass Guess) estimate involves a blend of intuition, experience, and limited available data. While it may sound informal, the SWAG estimate is a practical tool used in project management when precise data is unavailable. Initially, project managers leverage their past experiences and industry knowledge to make an educated guess about the project’s scope, timeline, and costs. This subjective approach helps in setting preliminary expectations and identifying potential challenges. Next, this initial guess is refined using any available data, however sparse it might be. Historical project data, similar project benchmarks, and expert consultations play a crucial role in this phase. Project managers analyze past projects of similar nature to draw parallels and make more informed estimations. They also consider the unique aspects of the current project that might affect the estimate, such as new technologies, differing team dynamics, or environmental factors. This process helps in transforming the SWAG from a purely intuitive guess into a more structured and reliable estimate. Finally, the SWAG estimate undergoes validation and adjustment through stakeholder review and iterative feedback. Engaging team members and stakeholders in the estimation process ensures that diverse perspectives and expertise are considered. Components Component Description Initial Intuition Leveraging past experiences and industry knowledge to make an educated guess about the project’s scope, timeline, and costs. Available Data Analysis Refining the initial guess using any available data, such as historical project data, similar project benchmarks, and expert consultations. Unique Project Factors Considering unique aspects of the current project that might affect the estimate, like new technologies, team dynamics, or environmental factors. Stakeholder Review Engaging team members and stakeholders to provide diverse perspectives and expertise, ensuring the estimate is comprehensive and well-rounded. Iterative Feedback Regularly reviewing and updating the estimate based on new information or changes in project scope to maintain accuracy and relevance. Historical Comparisons Analyzing past projects of similar nature to draw parallels and make more informed estimations. Expert Consultation Consulting with subject matter experts to gain insights and refine the initial guess with more precise and knowledgeable input. Preliminary Framework Creating a preliminary framework that provides a starting point for project planning and can be adjusted as more data becomes available. This table outlines the key components involved in developing a SWAG estimate. Pros & Cons While it provides a quick and intuitive starting point, it’s important to consider its advantages and disadvantages. The table below outlines the pros and cons of using a SWAG estimate. Pros Cons Quick to generate Lack of precision Leverages experience and intuition High degree of uncertainty Useful when detailed data is unavailable May lead to unrealistic expectations Helps initiate preliminary planning Relies heavily on subjective judgment Can be refined as more data becomes available Potential for significant adjustments later