Imagine the excitement of breaking ground on a new construction project—every detail planned, every resource allocated—only to watch deadlines slip and costs skyrocket.
It’s a frustrating reality for many, but the good news is, it’s avoidable.
Tracking the right Key Performance Indicators (KPIs) can be the difference between a seamless project and one that’s constantly firefighting.
These metrics aren’t just numbers; they’re your guide to staying on track and achieving success.
Take Schedule Variance, for example. With studies showing that large construction projects typically take 20% longer than expected, tracking this KPI can help you spot delays early.
Instead of reacting to setbacks, you can anticipate them, ensuring your project progresses smoothly and on time.
Cost management is another common challenge, with 85% of projects experiencing budget overruns averaging 28%. By keeping an eye on the Cost Performance Index, you can assess whether your spending aligns with your progress and avoid the pitfalls of financial mismanagement.
And then there’s safety, an area no one can afford to overlook.
Construction remains one of the most hazardous industries, with thousands of workplace injuries reported annually. Monitoring safety KPIs can help protect your workers while keeping your project on schedule and your reputation intact.
By focusing on these essential KPIs in a construction project, you’ll not only stay on track but also build a foundation of trust, efficiency, and success. These metrics are more than tools—they’re the compass that keeps your vision alive.
1- Schedule Variance (SV)
Time is one of the most critical resources in any construction project. Schedule Variance (SV) measures the difference between planned and actual progress, helping project managers pinpoint where timelines are slipping. For example, if a phase of the project was scheduled to complete in 30 days but has taken 35, the variance is a clear signal that adjustments are needed. This metric helps teams act proactively, minimizing delays that could cascade into larger issues.
However, SV isn’t just about identifying problems; it’s also a tool for better planning. Analyzing past variances allows project managers to refine future schedules, making them more realistic and achievable. Studies show that projects with regular SV monitoring are 40% more likely to meet deadlines. By keeping this KPI at the forefront, teams can stay aligned with client expectations and contractual obligations.
2- Cost Performance Index (CPI)
Managing costs in construction is notoriously challenging. CPI compares the budgeted cost of completed work to the actual cost incurred, providing a clear snapshot of cost efficiency. For instance, if the CPI value is less than 1, it signals overspending, prompting immediate investigation into cost overruns. This KPI is vital in large-scale projects where even minor inefficiencies can snowball into significant financial burdens.
Beyond current performance, CPI enables better forecasting and long-term financial planning. It allows project managers to adjust resource allocation, renegotiate supplier contracts, or implement cost-saving measures. By prioritizing CPI, construction teams not only manage their budgets effectively but also build trust with stakeholders by delivering cost-efficient results.
3- Earned Value (EV)
Earned Value is the heartbeat of project tracking, as it combines budget and schedule performance into a single metric. EV calculates the value of work actually completed compared to what was planned, helping managers identify if a project is on track. For example, if 50% of the budget is spent but only 30% of the work is completed, EV highlights inefficiencies immediately.
This metric goes beyond tracking—it empowers decision-making. With EV, project teams can reallocate resources to priority areas or adjust timelines without losing control. Many successful construction firms use EV to present stakeholders with a transparent view of progress, ensuring alignment between client expectations and actual performance.
4- Safety Incident Rate
Construction remains one of the most dangerous industries, with thousands of injuries reported annually. Safety Incident Rate measures the number of reported incidents relative to hours worked, highlighting areas where additional precautions are needed. A lower incident rate not only ensures worker well-being but also reduces downtime caused by accidents.
Focusing on this KPI also strengthens team morale and trust. Workers are more motivated and productive when they feel safe, and clients are more likely to choose contractors with a strong safety track record. By incorporating advanced training programs and safety technologies, teams can minimize incidents and maintain uninterrupted progress.
5- Labor Productivity
Labor Productivity measures the output of a workforce compared to the time and resources invested. For example, tracking how many units of work a team completes per day provides insight into efficiency. This KPI helps identify whether delays stem from underperformance or external factors like material shortages.
Improving labor productivity isn’t just about working faster—it’s about working smarter. Tools like task-specific training and advanced scheduling software can streamline operations, ensuring every hour on-site counts. Monitoring productivity also allows managers to reward high-performing teams, fostering a culture of excellence.
6- Budget Variance
Budget Variance tracks the difference between estimated and actual costs, offering a clear view of financial health. If variance increases consistently, it’s a red flag that costs are spiraling out of control. For instance, unexpected material price hikes or mismanaged subcontractor agreements often lead to budget deviations.
This KPI also serves as a learning tool. By analyzing variance patterns, teams can improve future cost estimates and avoid repeating mistakes. Projects with lower budget variance rates often attract more clients, as they demonstrate superior financial planning and reliability.
7- Change Order Percentage
Construction projects rarely go exactly as planned. Change Order Percentage measures the proportion of scope changes compared to the original contract. High percentages often indicate planning issues, while lower percentages reflect well-managed expectations and adaptability.
Tracking this KPI helps identify recurring issues, like incomplete designs or miscommunication with clients. By addressing the root causes of frequent changes, teams can improve workflows and build stronger relationships with stakeholders.
8- Equipment Utilization Rate
Idle equipment represents lost money. This KPI measures how efficiently construction machinery and tools are used, ensuring that assets don’t sit unused for long periods. High utilization rates indicate effective resource management, while lower rates suggest inefficiencies.
Optimizing equipment usage not only reduces rental or ownership costs but also extends the lifespan of machinery. Many successful firms use predictive maintenance and scheduling tools to maximize their equipment’s value, minimizing downtime and repair costs.
9- Rework Costs
Rework is one of the most expensive challenges in construction. This KPI calculates the financial impact of correcting mistakes, such as design errors or poor workmanship. High rework costs often signal deeper issues like inadequate training or communication breakdowns.
Reducing rework starts with preventive measures. Clear plans, thorough inspections, and better communication channels help teams avoid costly errors. By keeping rework costs low, construction firms can improve profitability and enhance client satisfaction.
10- Cash Flow Analysis
Cash flow is the lifeline of any project. This KPI tracks incoming and outgoing funds to ensure a project remains financially stable. Negative cash flow indicates trouble, as it limits the ability to pay for labor, materials, or unexpected expenses.
Effective cash flow management involves detailed planning and regular monitoring. Teams that prioritize this KPI can avoid disruptions, such as paused projects or strained relationships with suppliers, ensuring steady progress and financial health.
Track Your Construction Projects Instantly with Opteam
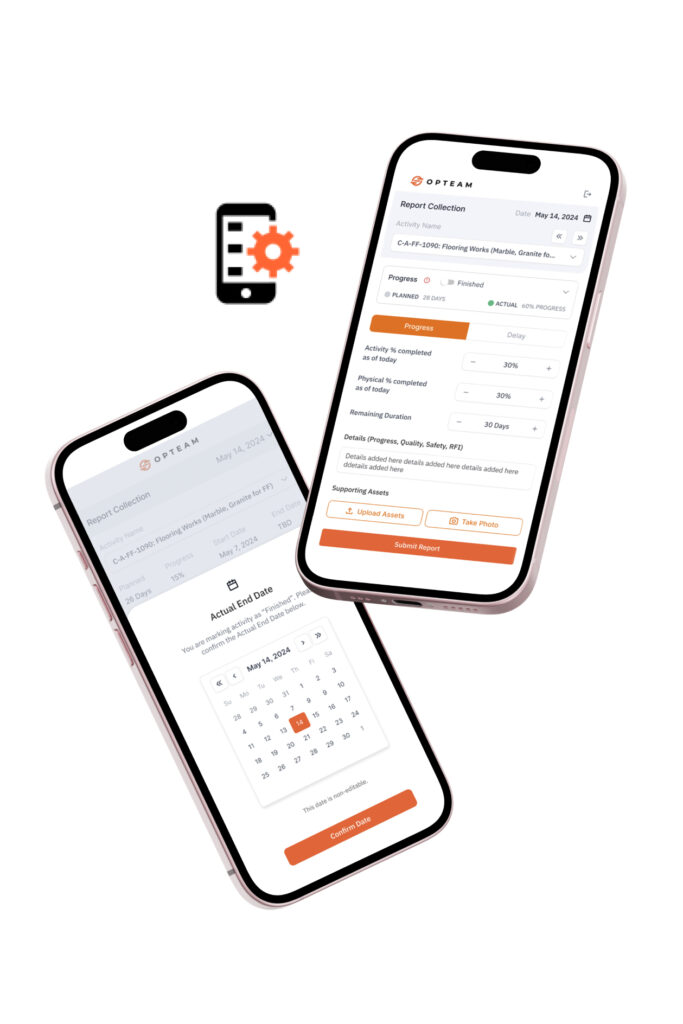
Managing construction projects has never been easier. With Opteam’s intuitive progress tracking software, you can monitor every detail of your project in real time, from schedules to budgets and resource utilization.
Designed for construction professionals, Opteam transforms raw data into actionable insights, helping you stay on track and meet your deadlines.
Whether you’re keeping an eye on schedule variance or ensuring cost performance, Opteam provides the tools to make informed decisions and optimize every aspect of your project.
Say goodbye to the chaos of manual tracking and scattered reports. Opteam’s user-friendly interface and advanced features ensure that your KPIs are always at your fingertips.
This means fewer delays, reduced rework costs, and a more efficient team. Ready to take your project management to the next level? Create your free account today and try Opteam free for 14 days—no strings attached.
Read more: