What is NCR Tracking In Construction?
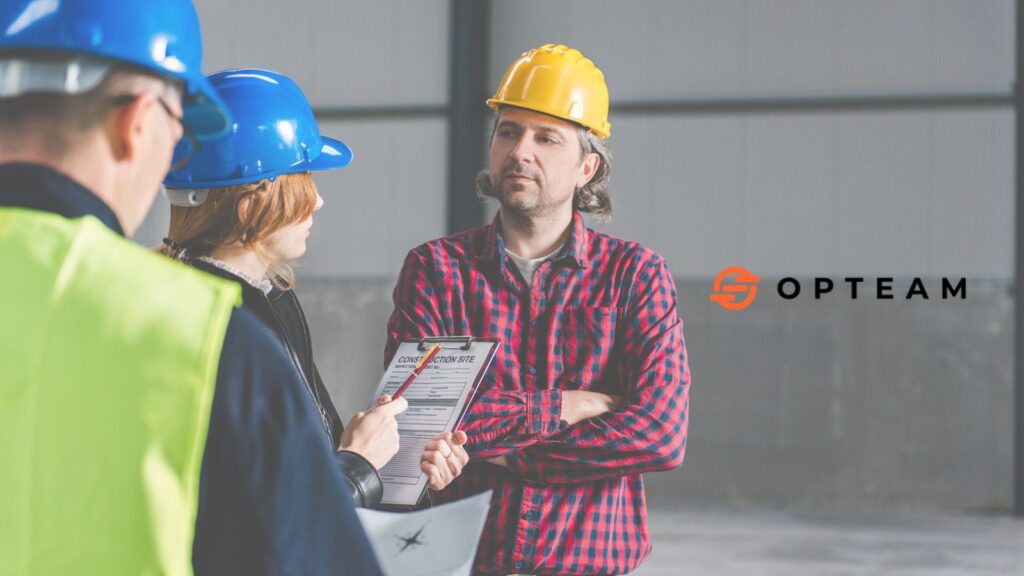
In short: NCR Tracking In Construction is a formal document used to identify and address instances where the work performed does not meet the specified standards, requirements, or project specifications. It serves as a critical quality control tool, allowing project managers, contractors, and stakeholders to pinpoint deviations from the agreed-upon plans, whether due to materials, workmanship, or other factors. By documenting these non-conformances, the NCR helps ensure that issues are promptly recognized and addressed to maintain the integrity and safety of the project. The NCR process typically involves identifying the non-conformance, describing the issue in detail, and proposing corrective actions to rectify the situation. This documentation is crucial for maintaining transparency and accountability within the project, as well as for continuous improvement in construction practices. The ultimate goal of an NCR is to ensure that all work adheres to the highest standards of quality and compliance, thereby minimizing potential risks and ensuring the successful completion of the construction project. ALSO CHECK Why NCR is needed in Construction Stages of NCR Tracking In Construction 1- Identification The identification stage is the first and critical step in the Non-Conformance Report (NCR) process in construction. This stage involves the detection and recognition of any work or materials that do not conform to the project specifications, quality standards, or contractual requirements. Identification can be initiated by anyone involved in the project, including site supervisors, quality control inspectors, engineers, or even subcontractors. It requires a keen eye for detail and a thorough understanding of the project’s criteria to accurately spot deviations. 2– Reporting Secondly, the reporting stage follows the identification of a non-conformance and involves formally documenting the issue in an NCR. This report includes a detailed description of the non-conformance, referencing the specific project requirements or standards that have been breached. Essential details such as the date of discovery, location, parties involved, and potential impact on the project are included. The report is then submitted to the relevant project stakeholders, such as the project manager, quality control team, or client representatives. Effective reporting ensures clear communication of the issue, enabling a structured approach to analyzing the root cause and determining appropriate corrective actions. This stage is crucial for maintaining accountability and transparency throughout the project’s lifecycle. 3- Evaluation Thirdly, the evaluation stage is where the non-conformance detailed in the NCR is thoroughly assessed. During this phase, the project team analyzes the root cause of the issue, considering factors such as material defects, procedural errors, or lapses in communication. This evaluation often involves input from various stakeholders, including quality control experts, engineers, and relevant subcontractors. The impact of the non-conformance on the project’s schedule, cost, and overall quality is carefully examined. This comprehensive assessment helps in determining the severity of the issue and the necessary steps to prevent its recurrence. 4- Corrective Action Fourthly, the corrective action stage focuses on developing and implementing solutions to address the identified non-conformance. Based on the evaluation, the project team devises a plan to rectify the issue, which may involve reworking the defective portion, replacing materials, or modifying processes to prevent future occurrences. The corrective action plan is documented in detail, outlining the specific steps to be taken, responsible parties, and a timeline for completion. Once the corrective actions are approved, they are executed under the supervision of project managers and quality control personnel to ensure they effectively resolve the issue. This stage is crucial for restoring compliance with project specifications and standards, minimizing disruptions, and maintaining the overall quality and integrity of the construction project. 5- Verification The verification stage involves confirming that the corrective actions taken have effectively resolved the non-conformance and that the work now meets the required standards and specifications. During this phase, quality control inspectors and project managers review the rectified work, often conducting tests or inspections to ensure compliance. Documentation of the verification process is crucial, including any test results, inspection reports, and photographs that provide evidence of conformity. 6- Closure Finally, the closure stage marks the formal completion of the NCR process. Once verification confirms that the corrective actions have effectively addressed the non-conformance, the NCR is closed. This involves documenting the resolution, including a summary of the corrective actions taken, verification results, and any lessons learned. The closure is officially recorded in the project’s quality management system, and all relevant stakeholders are notified. This final step ensures that the non-conformance is fully resolved and that the project can proceed without lingering issues. Typical NCR in Construction Who Decides What is a Nonconformity (or Non-Conformance) on Site? ALSO CHECK How to Manage and Track NCRs NCR tracking in construction involves several key steps to ensure issues are promptly addressed and resolved, thereby maintaining project quality and compliance. Here’s a structured approach: 1. Establish a Clear Process 2. Use a Centralized System 3. Regular Monitoring and Tracking 4. Effective Communication 5. Root Cause Analysis 6. Continuous Improvement 7. Audit and Compliance Preventative Measures to Avoid NCRs Conclusion In conclusion, effective management and NCR tracking in construction are crucial for maintaining quality and compliance in construction projects. By establishing clear processes, utilizing centralized management systems, and fostering effective communication, teams can efficiently address and resolve non-conformances. Regular monitoring, root cause analysis, and continuous improvement efforts further enhance the effectiveness of NCR management. Ultimately, by diligently managing NCRs, projects can mitigate risks, ensure adherence to standards, and uphold their commitment to delivering high-quality outcomes. This systematic approach not only resolves immediate issues but also contributes to long-term project success and client satisfaction.